An ultrasound train for an ultra-maintained rail network
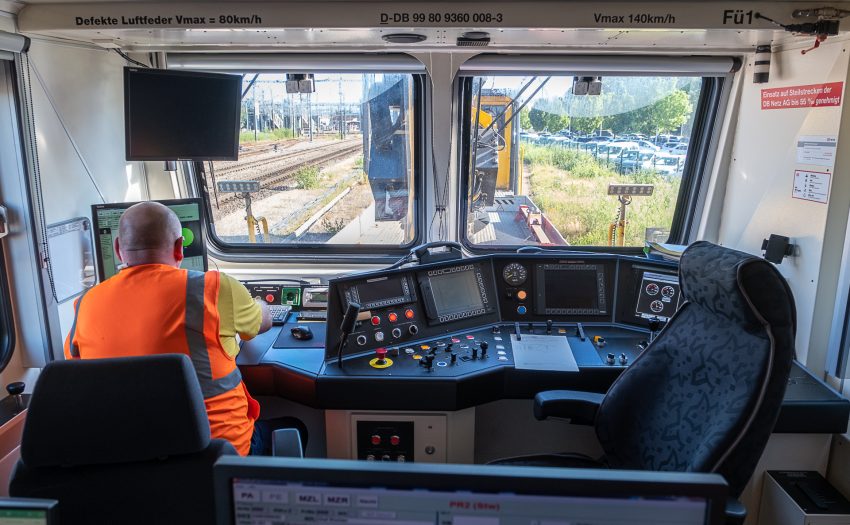
Twice a year, the CFL inspect the entire rail network using ultrasound techniques, with the support of a train and specialised tools. An effective method for detecting any defects in the rails and taking preventive action to ensure the safety and comfort of customers.
For humans, small problems or even the need for an intervention cannot always be detected with the naked eye, but with the assistance of a medical X-ray. This is where the medical X-ray procedure comes into play. The situation is similar with the rail network, where specialised equipment is also used.
Stationed on the edge of the CFL logistics centre in Bettembourg, the ultrasound train, belonging to the DB, is waiting for the starting signal, ready to take action, as can be seen from the tests carried out with water. Water is essential to ensure optimum connection between the train’s ultrasound equipment and the rails.
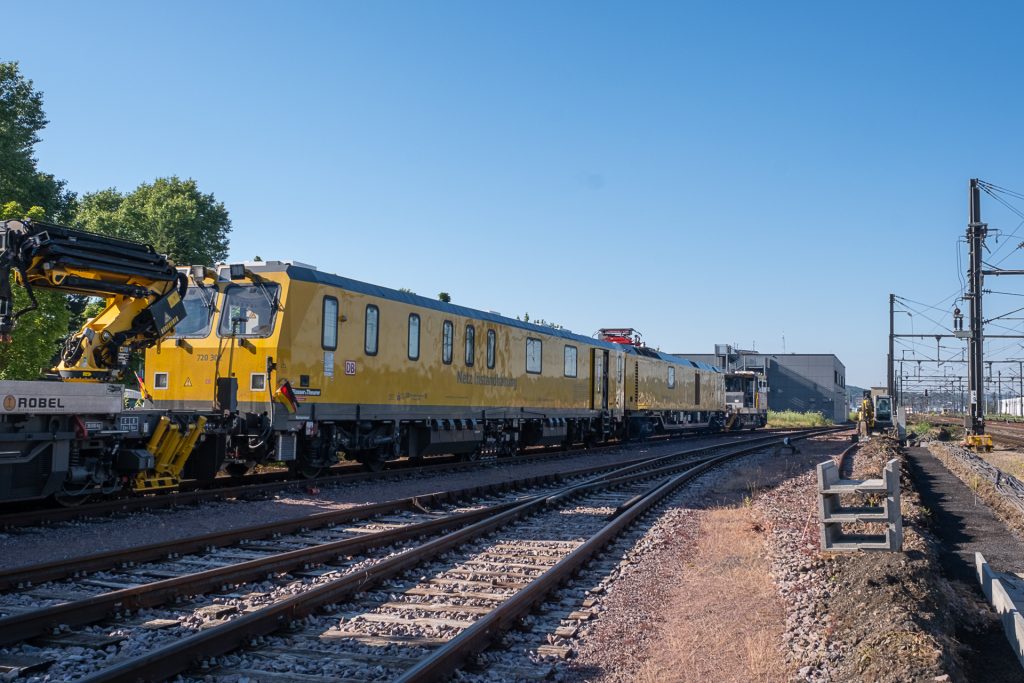

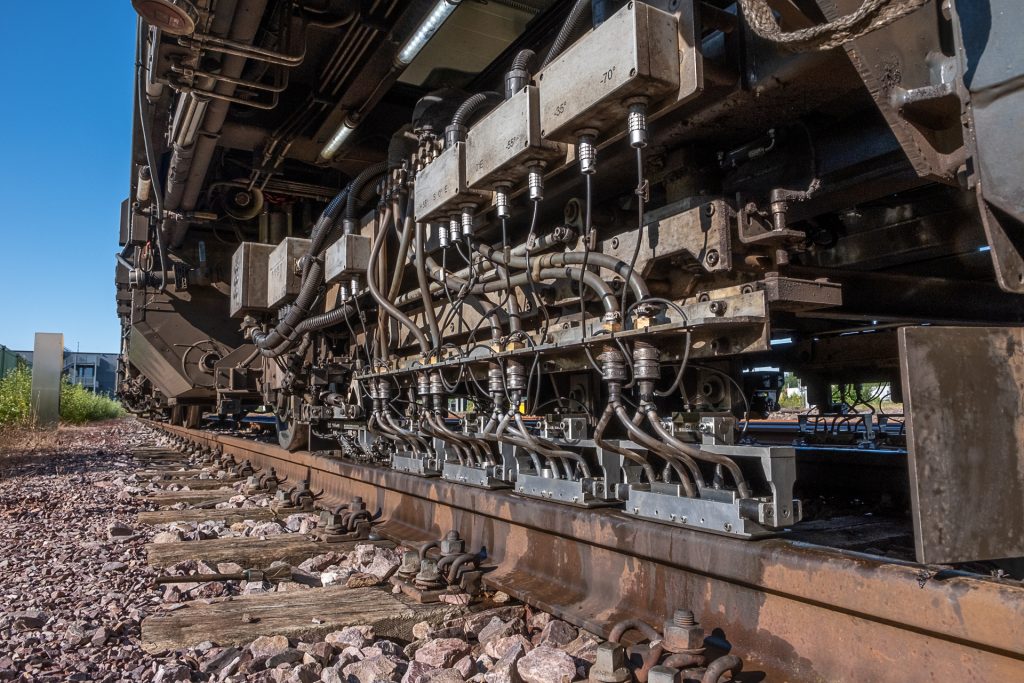
“Just as with an X-ray, no air must circulate between the measuring device and the body being measured, in this case the steel of the rail,” explains Ralf, Head of the Ultrasound team in the Infrastructure Maintenance Department of the CFL Infrastructure Manager. “We plan to run the ultrasound train twice a year over all the main tracks of the Luxembourg rail network. Each inspection planning is split into several days, with different routes depending on the passenger and freight traffic on each line, and to reduce any inconvenience to our customers to an absolute minimum.”
Inside, the DB experts are preparing for the last day of their four-day mission in Luxembourg, during which they will have worked and lived in this specially equipped train with state-of-the-art technical facilities, a repair workshop and comfortable accommodation.
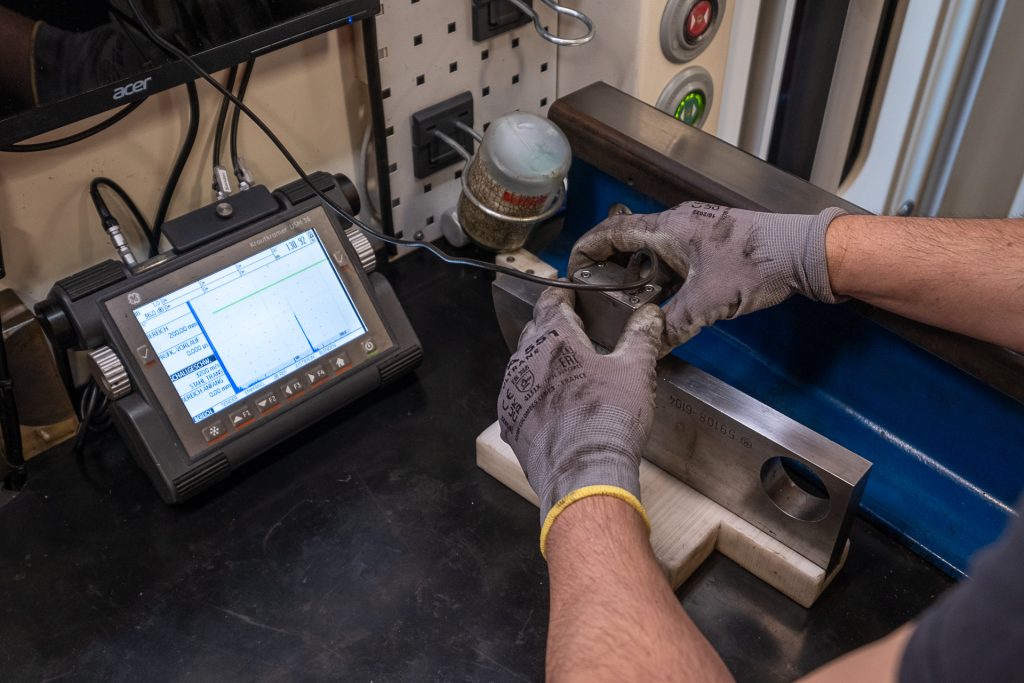
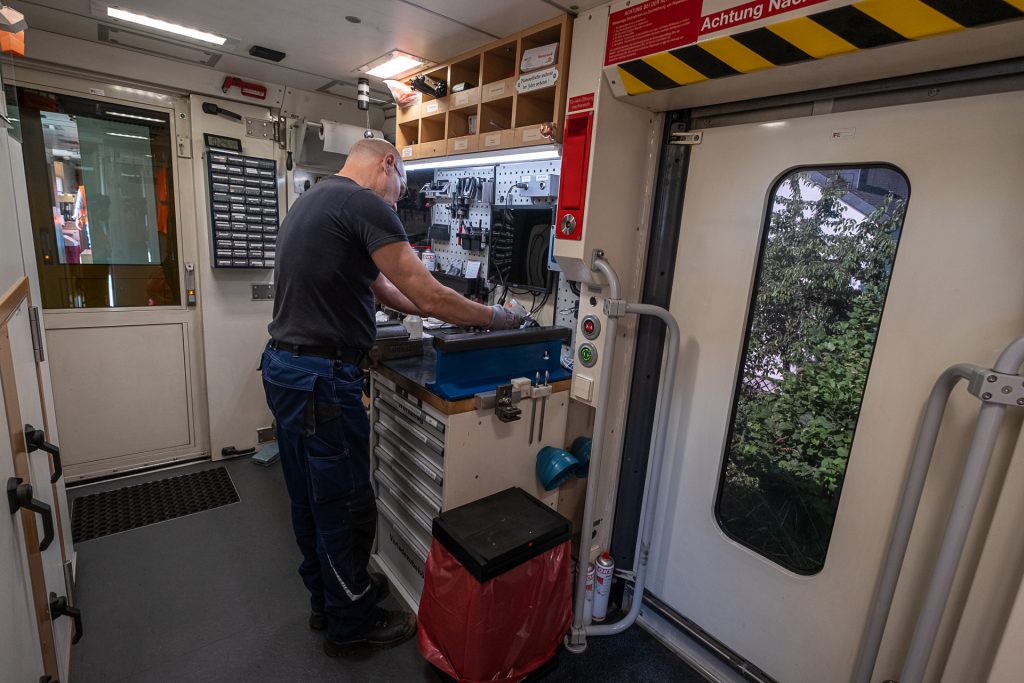
The signal is given by the CFL control centre regulating rail traffic. The CFL’s Robel engine goes into action to pull the ultrasound train, which does not have the necessary authorisation to run autonomously in Luxembourg.
All the layers of rail examined
Throughout the journey, that is made at a reduced speed (around 70 km/h), a DB agent visually checks, from the driver’s cab, the succession of kilometre points and marks them live on the control computer program.
In the middle of the train, one of his other colleagues has access to detailed information from the ultrasound frequencies. Each one inspects the rail at different depths, like so many layers broken down into interior and exterior. The CFL’s Trains and Rolling Stock Department also carries out ultrasound tests (using other equipment) during regular rolling stock maintenance.
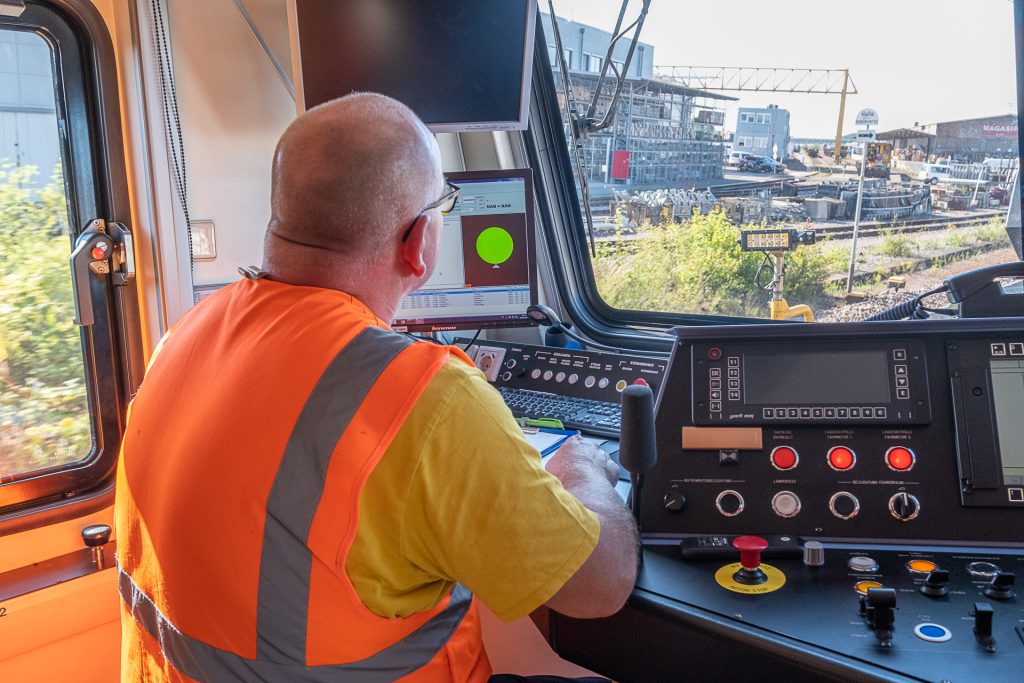
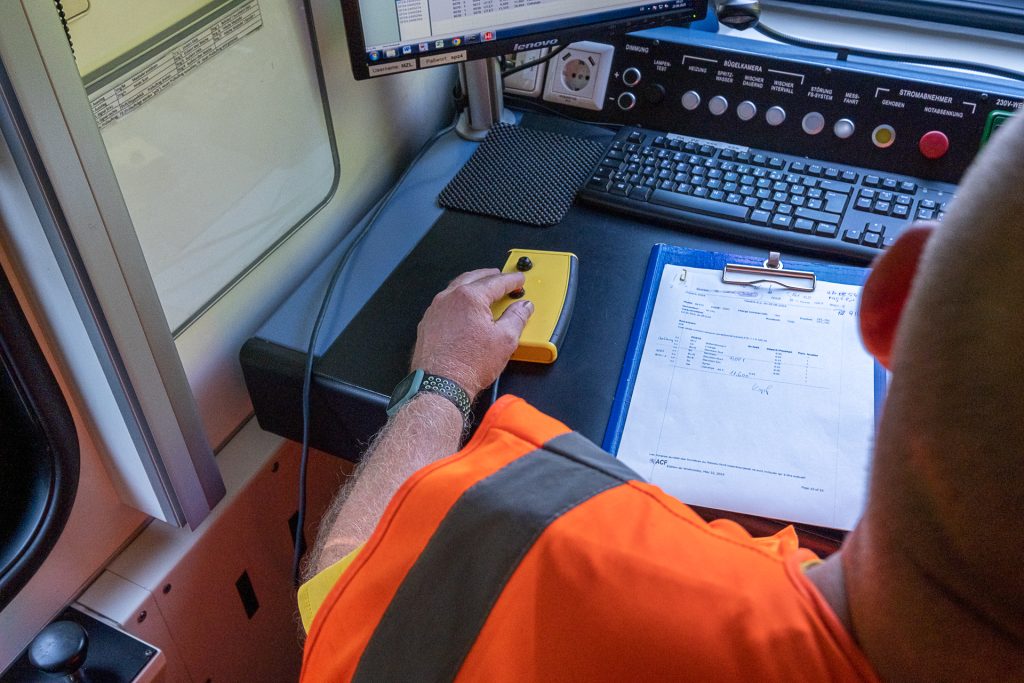
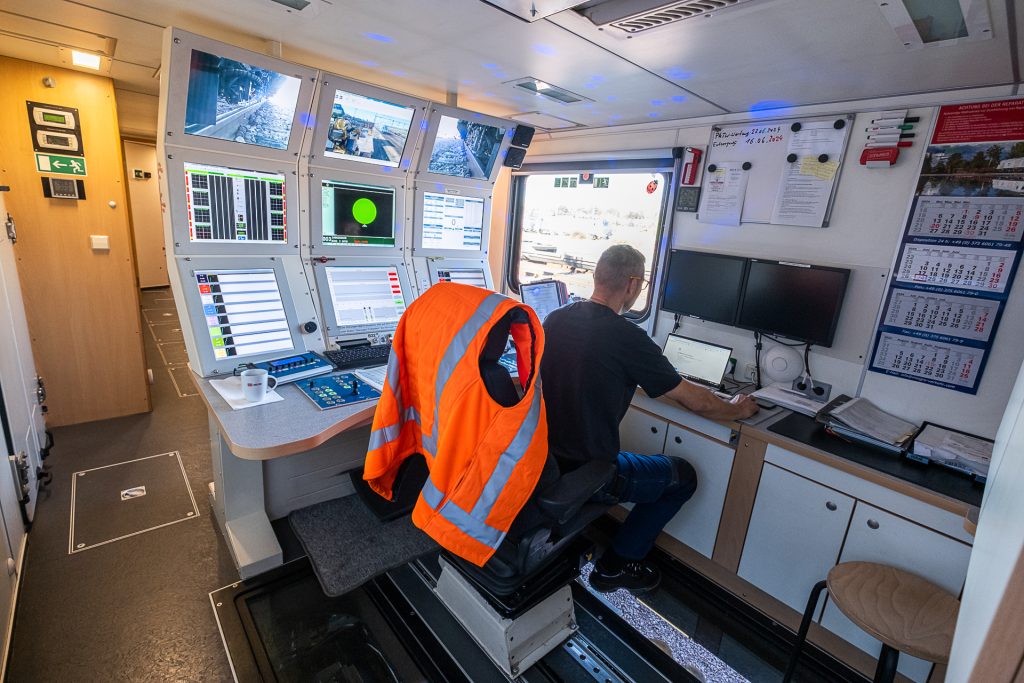
“Defects in a rail are often invisible and can come from a variety of sources,” explains Ralf. Some are caused by the manufacture of the rail itself and will develop over time, others are caused by the use of the rail in train traffic, while the expansion or contraction of the rail in winter or summer can also lead to defects.
Today’s mission consisted of inspecting two sections: from Bettembourg station to the French border (Luxembourg – Bettembourg – Thonville line) and between Berchem and Oetrange (Luxembourg – Wasserbillig – Trier line).
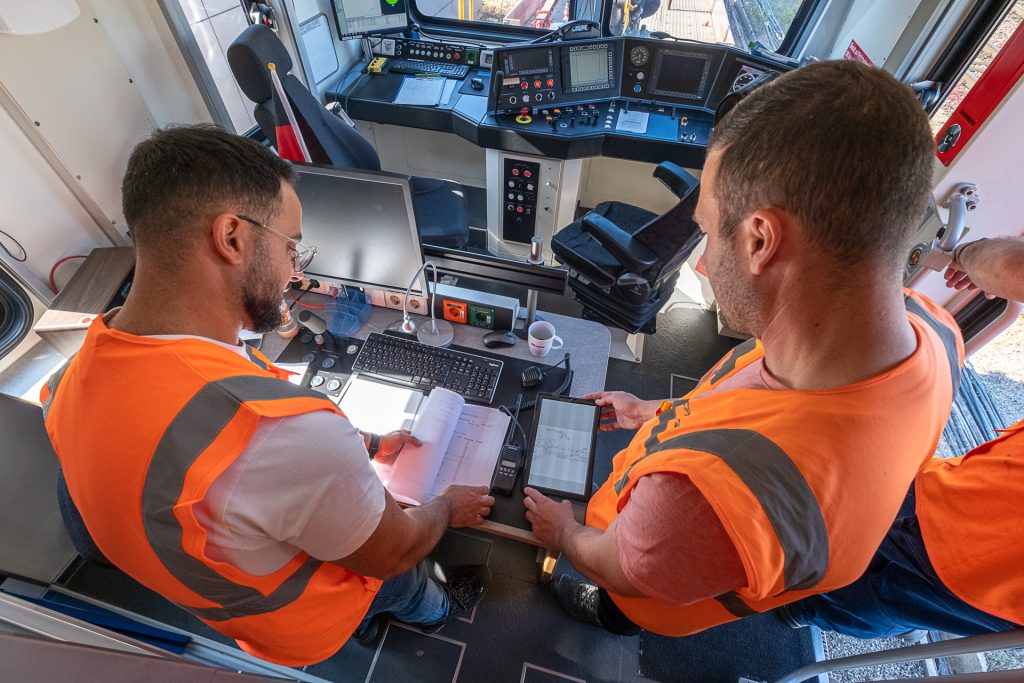
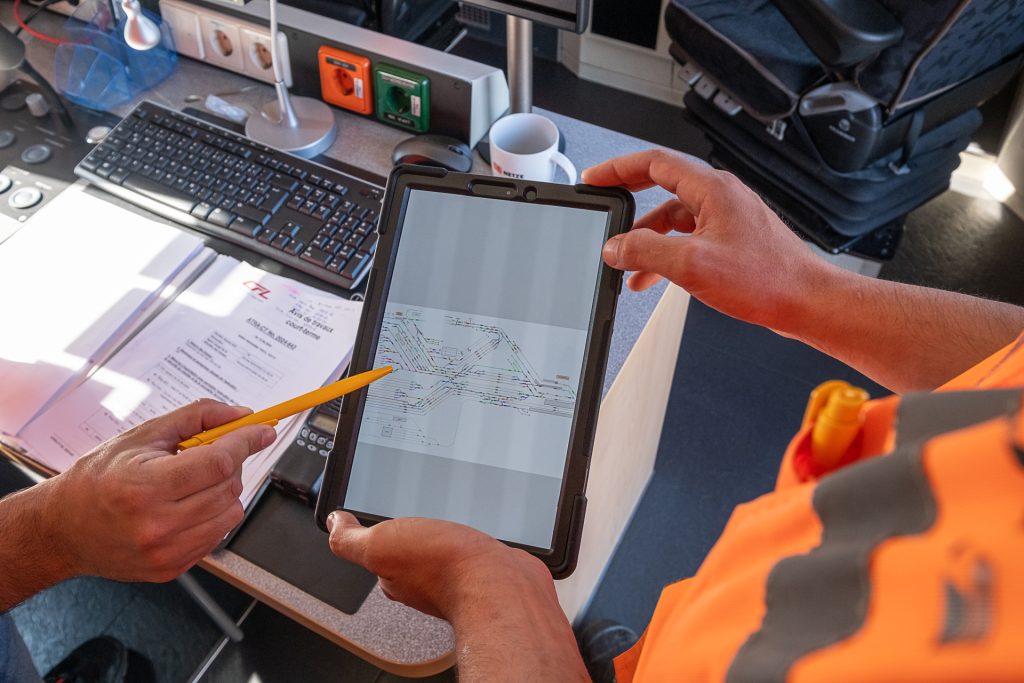
Two members of the CFL ultrasound team are present on each of these missions, enabling the CFL to receive an exhaustive report. Subsequent inspection results in a very low proportion of actual potential defects.
“Finally, we carry out manual checks using a draisian, also equipped with ultrasonic equipment, to confirm a defect that requires the replacement of a rail over a minimum length of 15 metres. These manual checks are also carried out in the freight handling areas, where many rails cross each other, and at the switches on the main lines of the rail network, where the ultrasonic train cannot run because permanent contact cannot be guaranteed,” adds Ralph.
Want to know how a switch works? You'll find the answer in this blog post: switches, simply explained.
A valuable mission for these experts who, like many of their CFL colleagues, work behind the scenes for the benefit of the CFL’s customers and staff: to guarantee quality of service and safety when travelling by train. In 2023, around 1.85 km of rail was replaced following the passage of the ultrasound train.
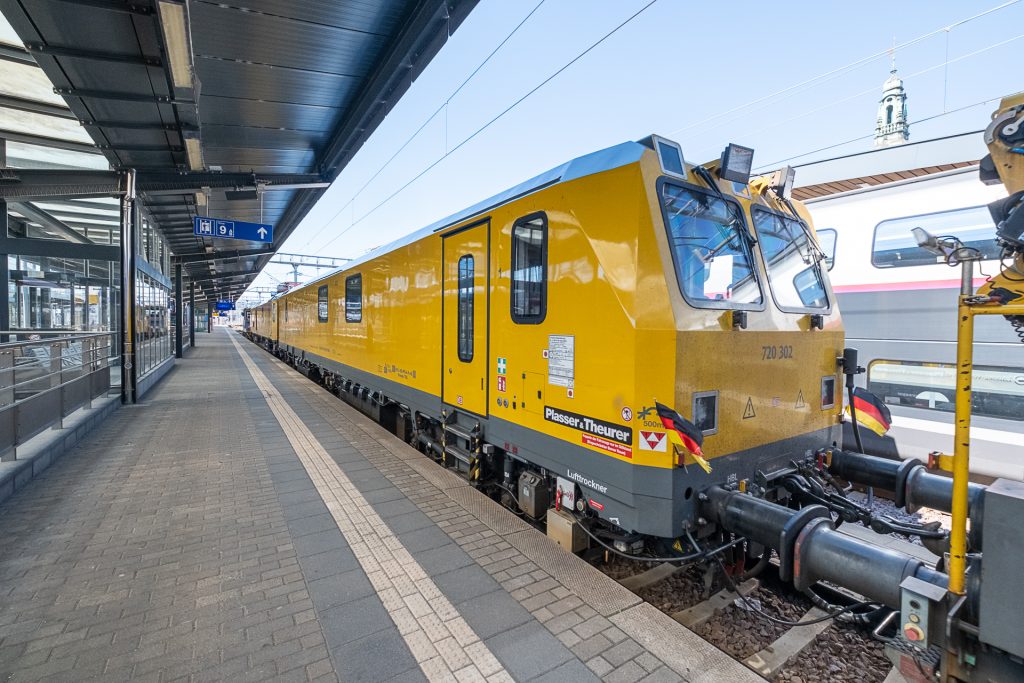