Extend service life and improve travelling comfort
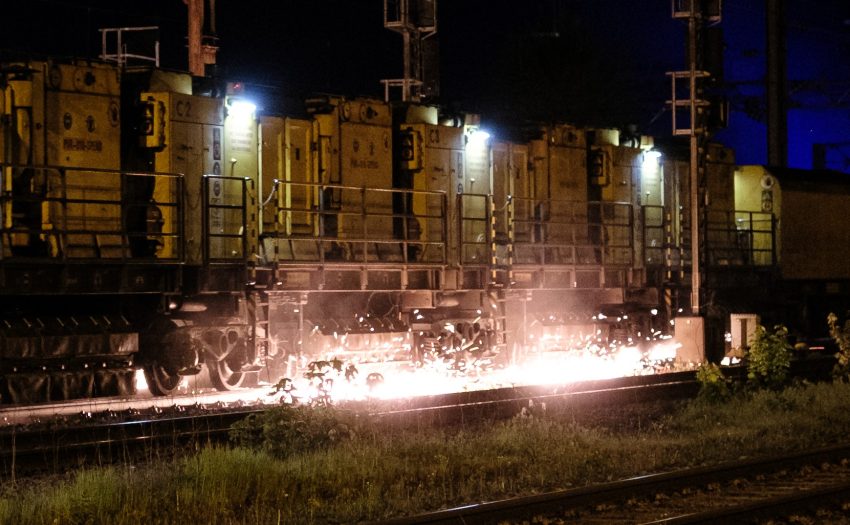
On duty with the SPENO rail grinding train
It’s age-old saying: good care and regular maintenance extend the service life. This also applies to rails: With careful maintenance, their life expectancy can double.
One example of careful maintenance as practised by the CFL is grinding the rails. ‘Without grinding, the service life is 15 to 20 years,’ says Kim Rohmann, Head of Cellule Voie. ‘If the rails are ground regularly, they last between 25 and 30 years.’
Annual workload is 80 kilometres
This work is carried out using a special train that the CFL hires from abroad. Where the SPENO, named after the Swiss operating company, is deployed is decided by prior inspections of the national railway company’s 630-kilometre-long track network. The rails are inspected every six months using an ultrasound train and checked for any irregularities; the teams also carry out visual inspections every two months.
‘We then decide on which sections of track we will utilise the services of SPENO,’ explains Kim Rohmann. ‘Around 80 kilometres of track undergo this maintenance every year.’
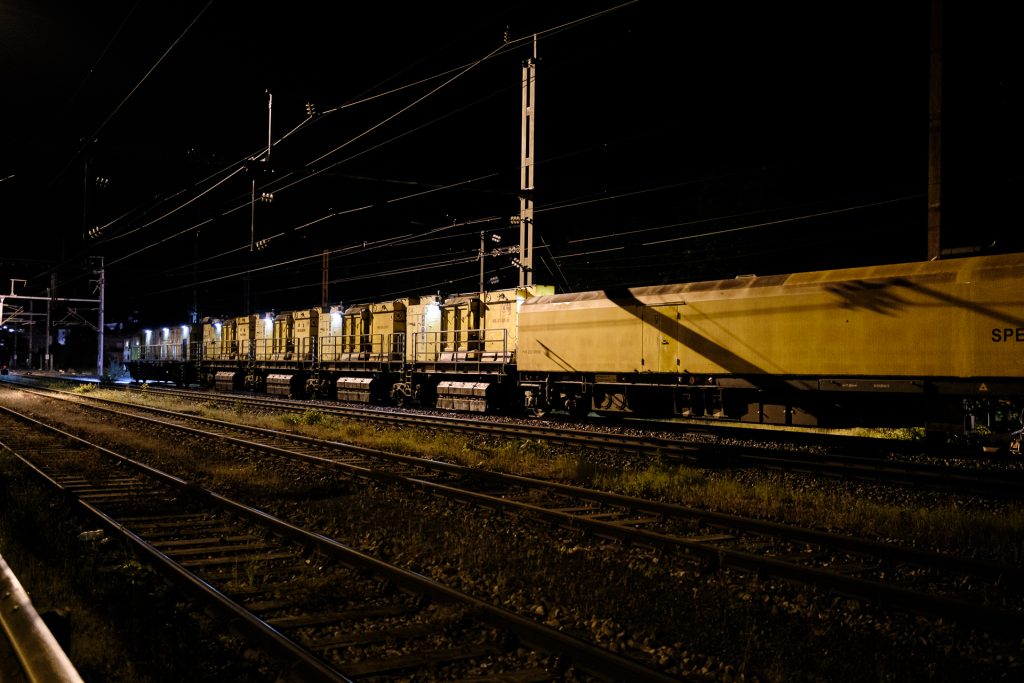
A benefit for passengers
In addition to extending the service life of the rails, the grinding process also ensures increased travelling comfort and a reduction in noise – which benefits passengers in their everyday lives. Michael Monteiro Da Silva, Deputy Head of the Cellule Voie, also points out the financial aspect: While maintenance with the grinding train costs around 600,000 euros a year, laying one kilometre of track costs 300,000 euros.
Depending on the condition of the rails, a distinction is made between curative grinding (up to three millimetres) and preventive grinding (over three millimetres). In addition to rail-wheel friction, Kim Rohmann cites the constantly increasing number of trains and their loads – ‘Freight trains cause more wear due to the high weight of the goods being transported’ -, speed and the track profile as the causes of rail wear. Particularly high-maintenance routes with many bends and a tight radius, such as the one between Kautenbach and Wiltz, require a lot of maintenance.
If very deep irregularities need to be repaired, a milling train is used instead of the SPENO. The approximately 1,000 switches are measured annually and, if necessary, ground manually.
A mission in Esch/Alzette
Mid-May, shortly after midnight. North of Esch/Alzette station, the SPENO is waiting for its turn – impatiently, as the sound of its engines suggests. The grinding work can only be carried out at night when regular train services are at a standstill. Like all work carried out at night, it is a race against time, as the track has to be cleared for rail traffic on time. ‘We can grind between 500 and 600 metres of track in an hour,’ says Michael Monteiro Da Silva, describing the time challenge. ‘Ideally, we have between four and five hours available.’
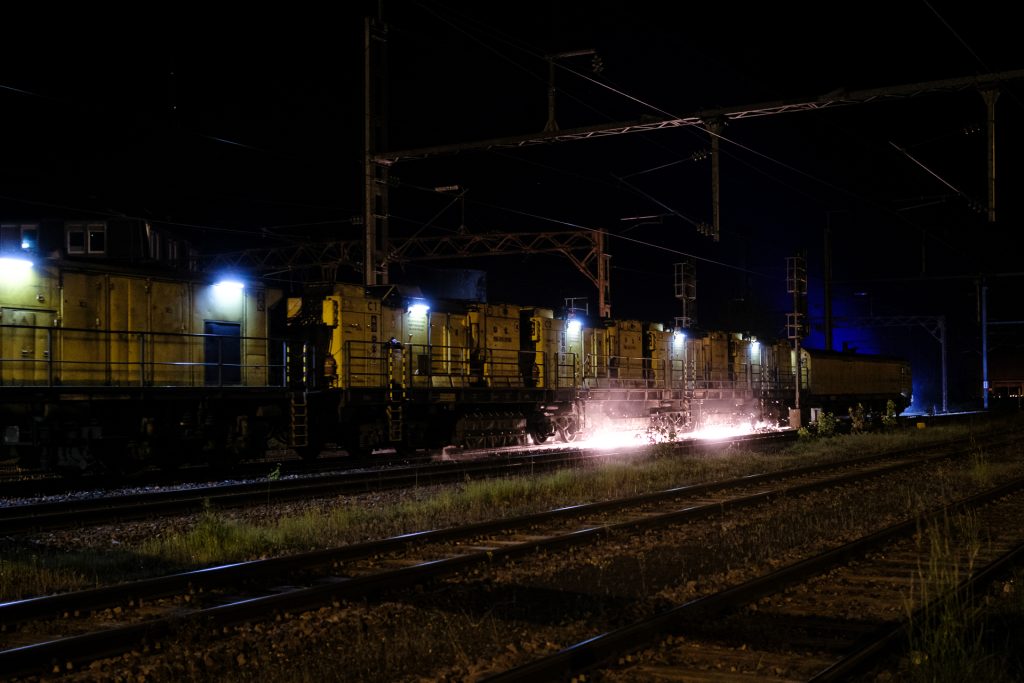
He himself obtained the necessary permits in the weeks leading up to the project and had leaflets distributed to local residents informing them that it would be a little louder at night. The crew on duty at night remove cables, signals and instruments, such as axle counters, from the rails shortly before the grinding work begins. The aim is to avoid unnecessary damage.
At around 01.30, the last freight train passes the line. The SPENO’s diesel engines are immediately revved up, black smoke rises into the dark night, the train moves into position and sets off immediately afterwards. The grinding stones mounted in pairs under the train are lowered onto the rails and, like a fire-breathing dragon, the machine glides noisily along its working track. Protective tarpaulins attached to the flanks prevent sparks from flying too high. Spray jets under the train and water lances at the ends of the train eliminate the risk of fire, especially if the rails are still resting on wooden sleepers and there is a lot of vegetation along the track.
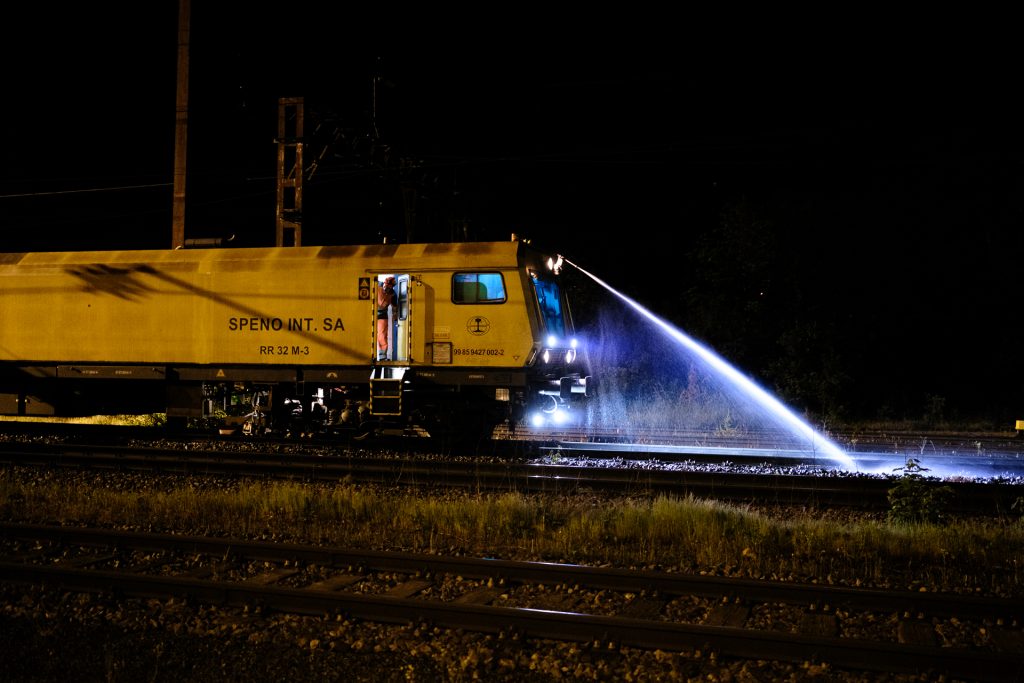
The grinding process is repeated several times. How often is determined by sensors that record the condition of the rails and transmit it to the driver’s cab. After around half an hour, the night’s work is done. The SPENO is re-connected to a CFL maintenance train – the grinding train is only allowed to travel on the Luxembourg network with the ETCS-equipped railway maintenance machine – and driven to Bettembourg, the railway line is prepared for train traffic again.
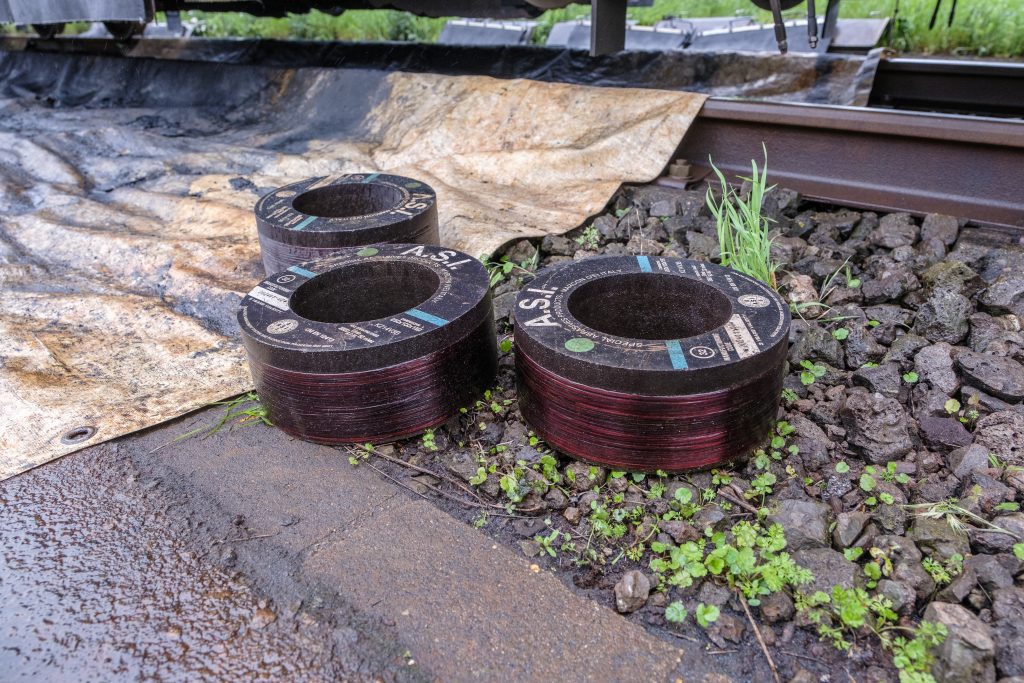
The SPENO also needs maintenance
Like the rails, the rail grinding train also requires maintenance. Before it is used again, the 266-tonne, 77-metre-long yellow track maintenance train is cleaned at the Centre Logistique de l’Infrastructure Ferroviaire (CLIF) in Bettembourg. Covers and panelling are removed and the units are cleaned with compressed air jets. The importance of this is demonstrated by the material that is removed and has to be disposed of.
The 32 grindstones are inspected and replaced depending on how worn they are. A process that the SPENO team carries out quickly and skilfully. After that, nothing stands in the way of a new grinding job.
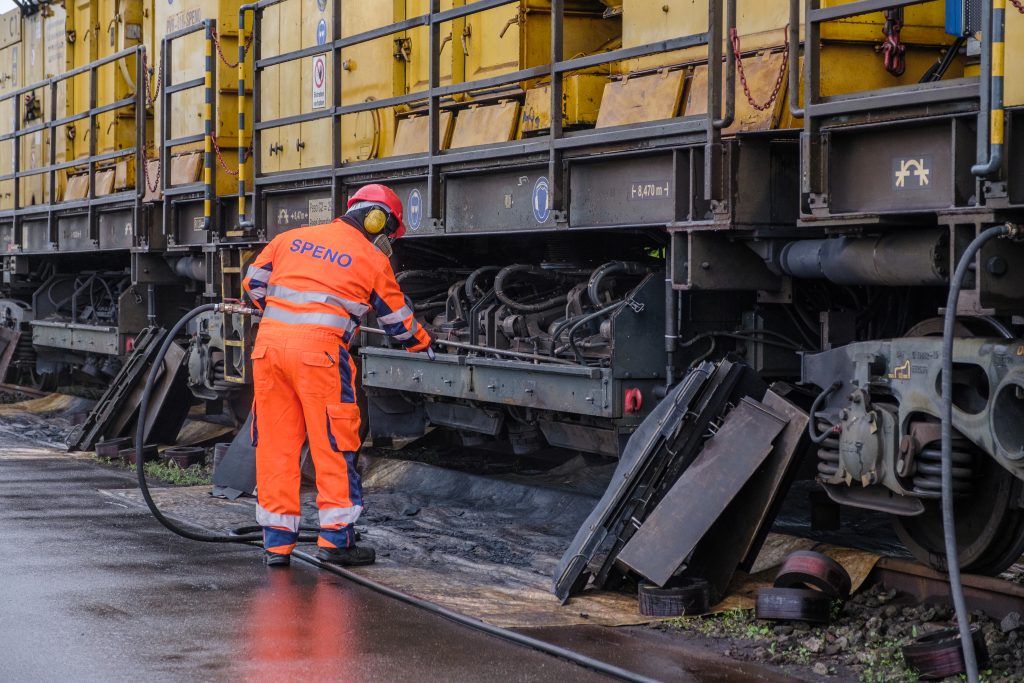
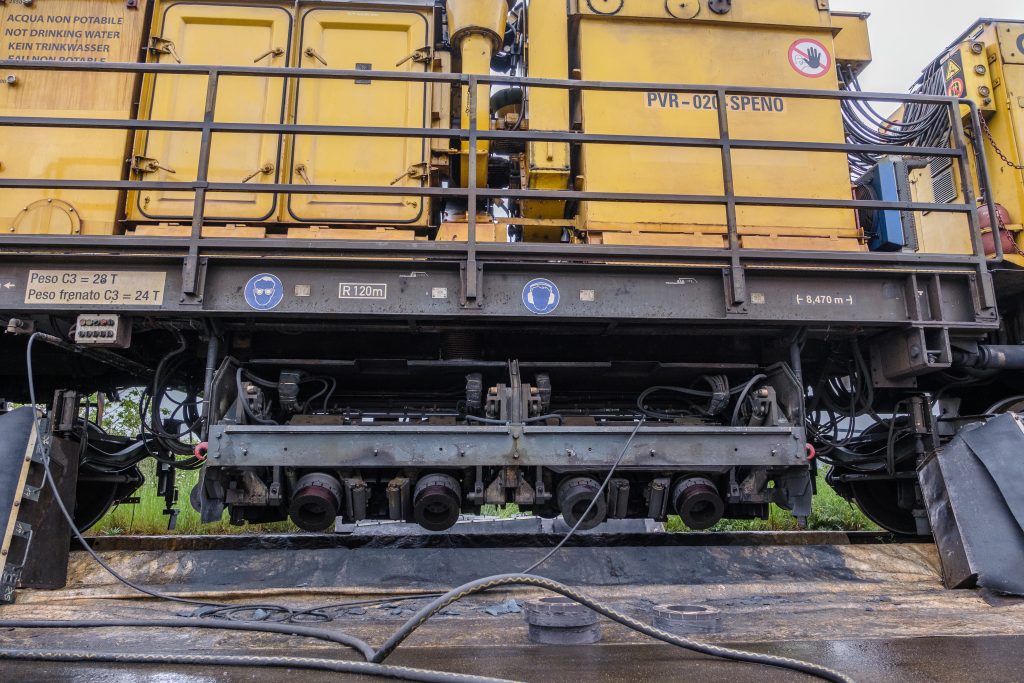
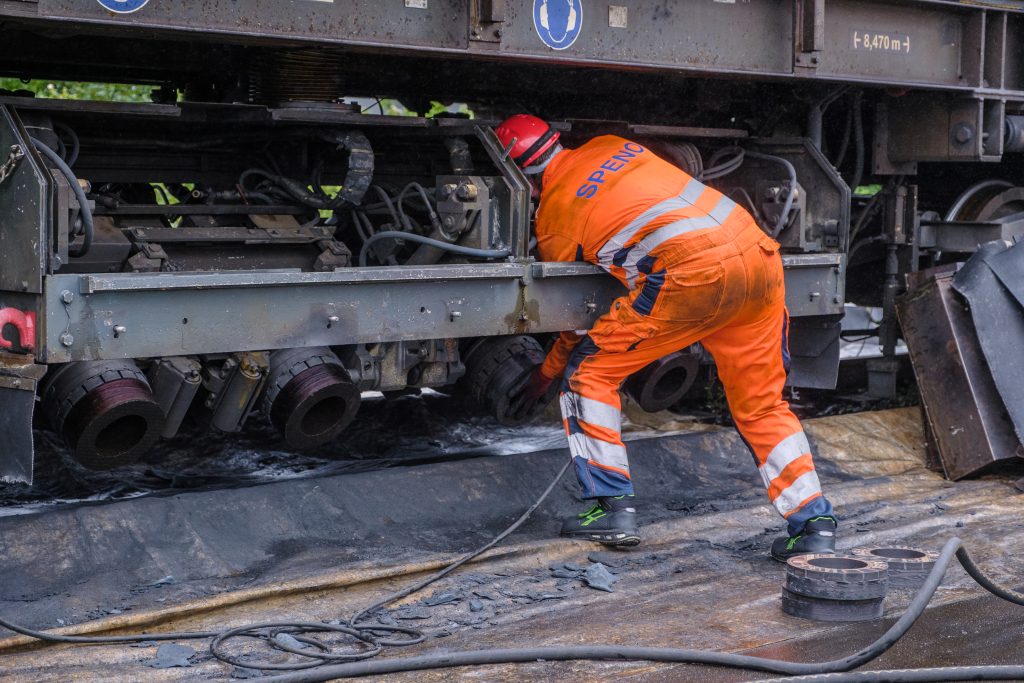
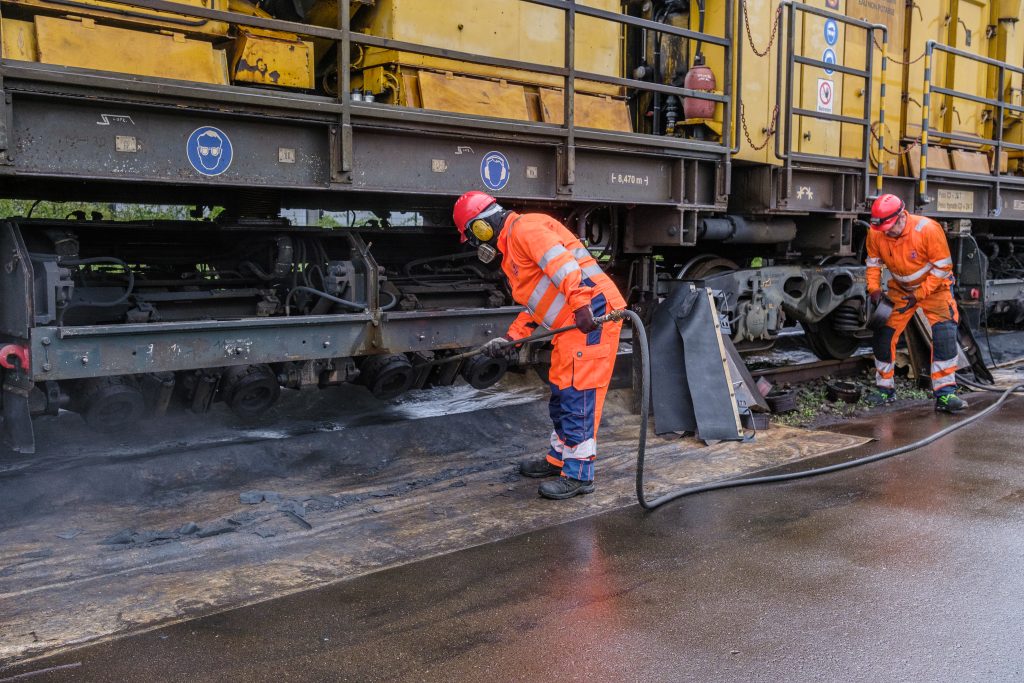