Behind the scenes at the CRM, the nerve centre of CFL’s train mechanics
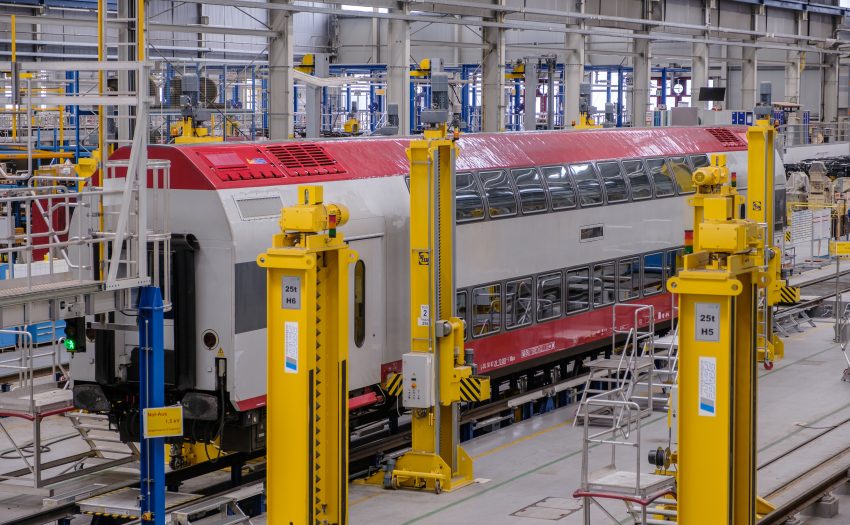
Every day, the 300 employees of the CFL’s Repairs and Maintenance Centre (CRM) optimise train repairs and maintenance operations. A culture of continuous improvement which is focused on customer service.
At the heart of the CFL’s Repairs and Maintenance Centre (CRM) in Luxembourg-Bonnevoie, safety, quality and productivity go hand in hand. By combining these three elements, the teams ensure the availability of rolling stock for the needs of the CFL Operations Centre, which is responsible for putting the rolling stock into circulation on the rail network.
“One of the key factors in boosting productivity is to stay focused and work at an appropriate pace, without neglecting safety or quality – quite the contrary!” sums up Guy Lux, Head of the CFL CRM (Trains and Equipment Department).
On the 16 maintenance tracks of the Central Workshop and the Rapid Repair Centre, some 300 maintenance technicians and engineers are mobilised day and night, 7 days a week, to serve the ever-increasing number of customers on board CFL trains. “We always keep in mind the ultimate aim of our work, is to provide our customers with a mobility service that they can board a train in perfect working order,” adds Guy Lux.
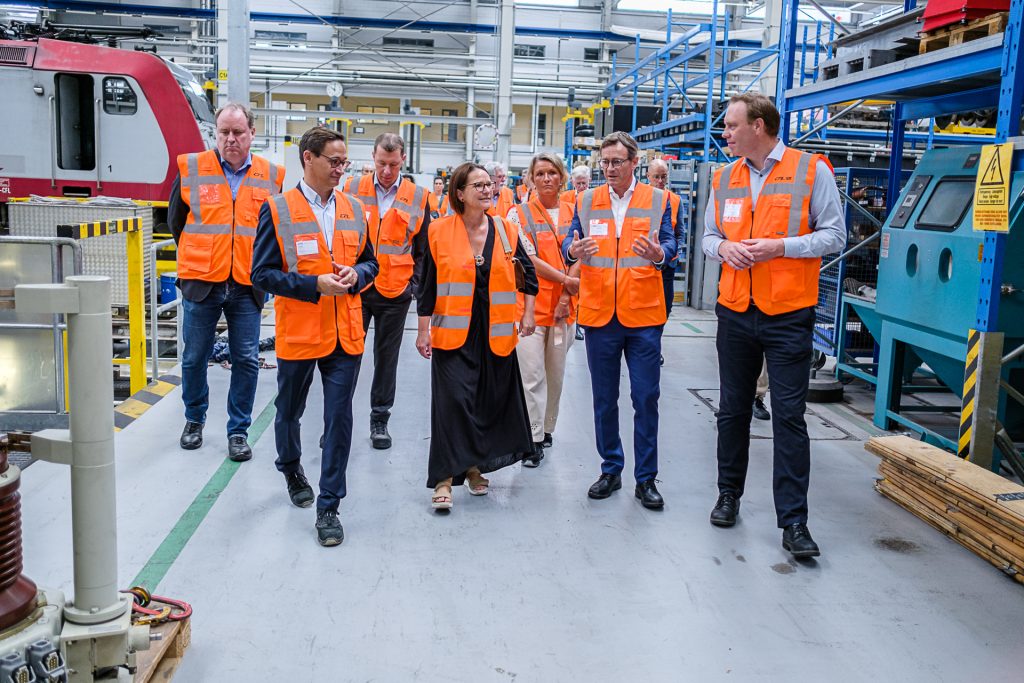
Communication, organisation, technology
Every day is a blank page, between scheduled maintenance – depending on the mileage or life cycle of the train – and breakdowns of varying degrees of seriousness that need to be dealt with as quickly as possible.
“The human factor, in this case the know-how of our teams, is essential to the success of our missions”, Guy Lux emphasises. The Head of the Maintenance Centre and one of his managers, Carlos Gonçalves Leite (Production Manager), instill an organisation in the field based on transparent communication and the empowerment of each person, with attention to detail in the execution of tasks.
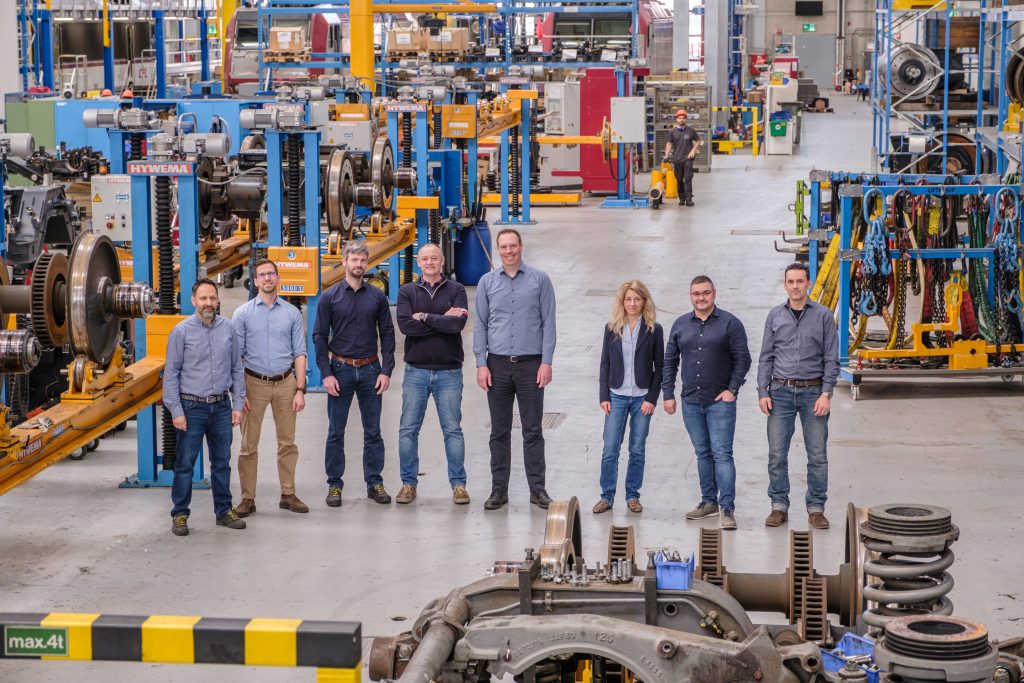
“We bring all our operational managers together twice a day to facilitate feedback and adjust our planning, which results in maximising our work resources,” adds Guy Lux. With one objective in mind: to leave no rolling stock unattended.
“Thanks to the analytical work of our engineering department and our technological tools, we are able to fine-tune diagnoses and interventions according to the type of rolling stock,” notes Guy Lux. Efficient repairs and maintenance mean improved reliability, as we are seeing a drop in breakdowns on trains in service.
This work is bearing fruit: by 2023, 99% of the trains required by the CFL Operations Centre were available. Last year, an average of 12 trains passed through the Central Workshop every day.
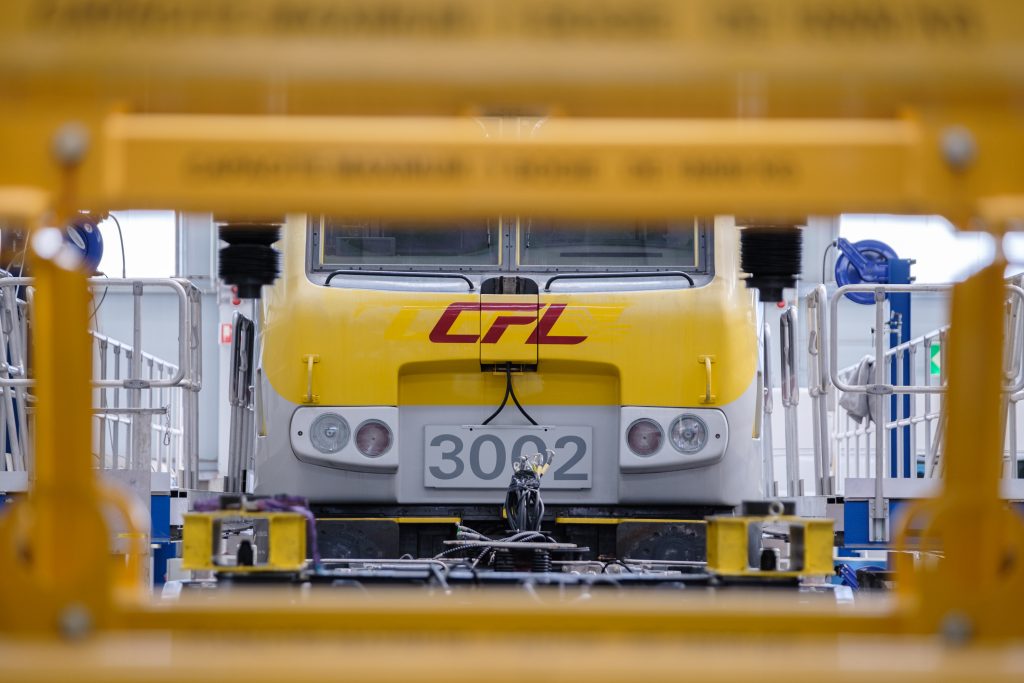