CFL’s new workshop: 15.000 square meters to impress
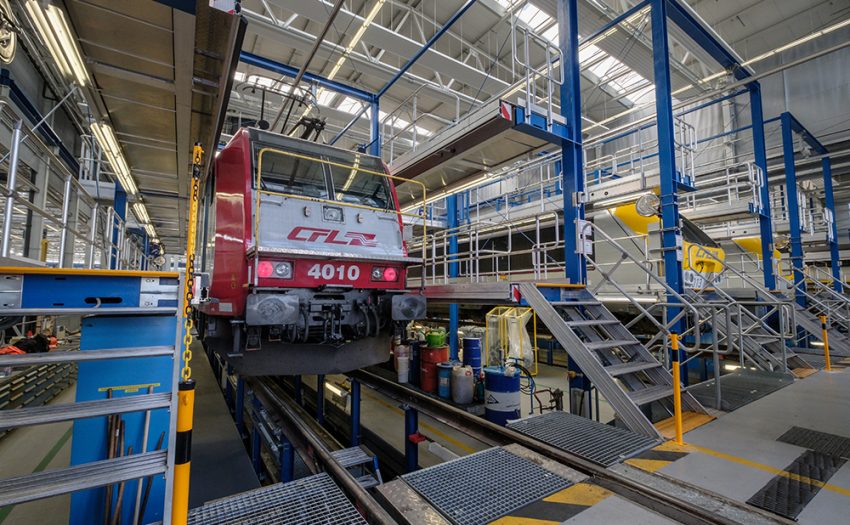
Everything (and everyone) under one roof
The new Atelier Central has one large and distinct advantage: For the first time since the company was founded, it is now possible to maintain the entire spectrum of CFL rolling stock under one roof. Approximately 15,000 square metres of space and 1,250 track metres (indoor and outdoor) are available for this. In the new premises, therefore, maintenance and repairs are carried out on both EMUs, i.e. rail cars without locomotives and with own drives, electric locomotives, and the modern, high horsepower 4000 series, double-decker passenger cars, as well as railway vehicles with diesel electric motors, e.g. the Robel construction site engines.
- The maintenance of CFL’s power bundle with more than 7,000 bhp is also completed inside the new workshop : a 4000 series locomotive of Bombardier.
- The necessary infrastructures for the maintenance of electric railcars are also available in the new workshop.
- The maintenance of the rolling stock powered by diesel engines, like this Robel construction vehicle, can also be handled under one same roof.
The staff of the new Atelier Central also benefit from a modern working environment that leaves little to be desired, and which has been tailored to the needs of the different teams. The new workshop scores with comfortable light conditions, both by day and by night, a good indoor climate as well as modern workplace installations, e.g. work platforms and lifting devices. Thus, the new working pits offer not only plenty of space, but are also bright and heated.
- The working pits of the new Atelier Central…
- well lit and heated.
Moreover, an uncompromising respect for occupational safety also played an important role in the design of the workspaces. Access to the roofs of the electric-powered locomotives and railcars, for example, is ensured using an extremely well-designed safety system that only allows the overhead lines in the halls to be switched on when all staff have been withdrawn from the danger zone.
The Atelier Central: collective know-how
Among those working on the maintenance and repair of the rolling stock in the Atelier Central are mechanics, electrical engineers, as well as refrigeration and electronics specialists. Also on site is a joinery, saddlery and infirmary. Around 280 employees work in the “Centre de Remisage et de Maintenance”, which includes the new Atelier Central, the “Centre de Réparation rapide”, and the washing plant, where they look after around 178 different vehicles.
- The maintenance of the pantograph : part of the work done inside Atelier Central.
- The maintenance of the brakes : a must in view of the weight of several tons!
- During the maintenance of the rolling stock, the axle geometry is also checked…
- just as the cooling and A/C technology are…
- In order to guarantee the comfort of customers and staff at any time.
- Electronical, electromechanical and communication technologies play a more and more important role in view of the modern rolling stock.
Need to store 15,000 different parts? Challenge accepted!
The size and variety of its fleet presents CFL with a number of logistical challenges. More than 15,000 different parts are needed for the maintenance and repair of the various vehicles. A sophisticated logistics system helps the company maintain an overview of everything. All items are individually recognized, catalogued and assigned a number/QR code. If this number is entered in the display of the Kardex logistics system (automated carousel), it independently searches for the required part, which shortly thereafter is presented to the parts warehouse specialist on an aluminium tray. Larger and above all heavier spare parts are stored on metre-high pallets and space-saving shelves. These too are inventoried, but due to their size and weight have to be lowered or lifted with side-fork forklift trucks.
- The Kardex Remstar, master-piece of logistics. Several thousand parts are available by a simple push of a button…
- Simply enter the part number using the system’s display…
- and the required part is served on an aluminium platter.
Maintenance of the bogies – large springs, and an even larger effect
Many people are unaware of the fact that modern rolling stock nowadays consists of an upper part and a lower part – the bogie. By decoupling the lower chassis from the upper box, any unevenness in the track infrastructure can be better absorbed and the comfort of customers is maximized. The bogies are equipped with sophisticated suspension systems that require regular inspection, including of their suspension properties. This is carried out in special machines in which the XXL springs are clamped, compressed and tested.
- Thanks to special jacks, 12 in a row with a lifting capacity of 25 tons each, the rolling stock is lifted up for maintenance reasons.
- This is for instance necessary for the maintenance of the bogies (in this picture the bogies of double-decker driving trailer).
- Once the screws connecting the bogie and the upper part have been loosened, the two elements can easily be separated.
- Only the upper part of the trailer remains on the jack.
- The bogie is lifted up by crane to the maintenance area.
- The bogies’ shock absorbers are uninstalled and their suspension properties are tested in this machine.
- After its maintenance, the bogie is awaiting its reinstallation.
- The upper part and the bogie are connected by means of screws. Some of them with a torque of up to 1000 Nm, which corresponds to 10 times the torque needed to tighten the screws of a car tire.
Until the sparks fly – the new underfloor lathe
A special highlight of the new Atelier Central is the new underfloor lathe. Thanks to this innovative device, it is possible to re-sharpen the profile of the rolling-stock wheel sets without having to remove the bogie, i.e. the part with wheels that is located beneath the passenger cars and the locomotives. This saves time and money.
The so-called re-profiling of the wheel sets is a science in itself. This is because only a correct profile will ensure that there is no unnecessary friction between the wheel and the rail while turning. Any slight deviation in the angle between the tread and the rail impairs the wheel contact – something then noticed by passengers as the cars roll from side to side or bump up and down. In order to restore the required angle, the computer-assisted underfloor lathe removes tiny parts of the wheel set – a process that is associated with intense heat and sheaves of sparks!
- Thanks to the underfloor lathe, the reprofiling of the wheels can be effectuated without the uninstall of the wheelsets.
- To achieve this, the wheelsets are lifted up…
- their profile is analyzed …
- and the necessary amount of material is removed in order to create the perfect angle between the running surface of the wheels and the rails.
- As only millimeters are removed, the process is computer-controlled.