Continuous improvement through recycling
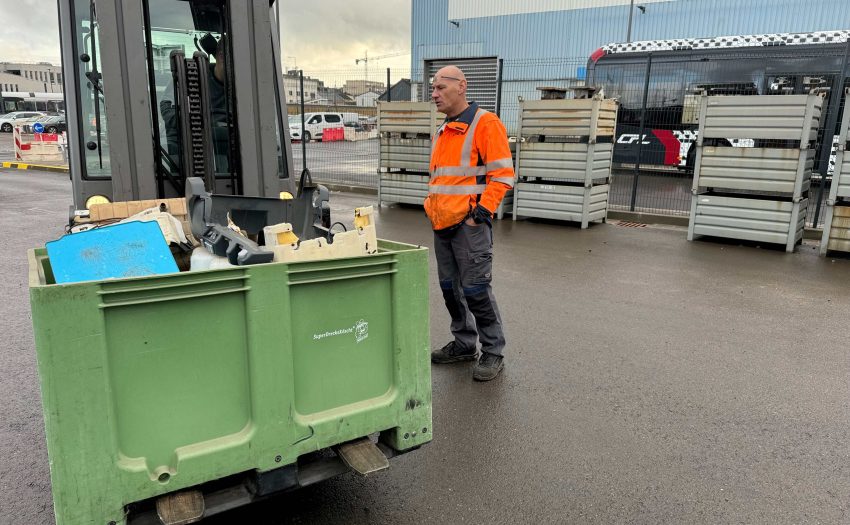
The CFL sorting centre acts as a point of expertise for the recycling of Central Workshop and Bus Service equipment. It has become an indispensable interface that is adapted to internal needs, in collaboration with its main partner: SDK fir Betriber.
During the European Week for Waste Reduction (16-24 November 2024), we take a closer look at a tailor-made infrastructure created by the CFL, reflecting the Group’s commitment to the environment: the Recycling Centre.
Since 2020, the Recycling Centre has been housed in new facilities at Bonnevoie, on the site of the CFL Repairs and Maintenance Centre (see also: CFL Central Workshop). A logical move, given that this unit, staffed by four people, receives equipment from the Central Workshop and the neighbouring Bus Department throughout the day. Equipment that has already been sorted and handled by colleagues in these departments.
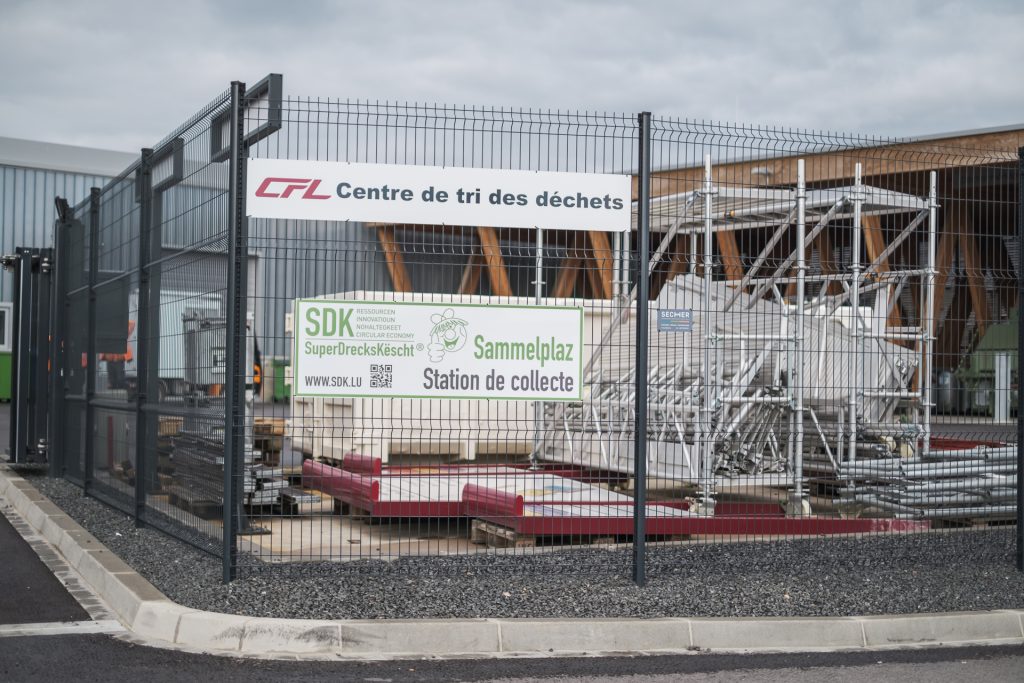
From sand to bogie dampers
At first glance, the Recycling Centre may look like a recycling centre accessible to the general public, with various shelves and areas for sorting and storing waste, but it is in fact an infrastructure that has been totally designed with the CFL’s activities in mind. In addition to conventional materials such as plastic, frigolite and cardboard, which are received before being recycled, various materials specific to the rail sector are handled here.
‘We receive user sand, for example, which is used in the traction and braking systems of trains,’ explains Patrick, head of the Recycling Centre. ‘We also receive a lot of cable waste from servicing and maintenance work, and laminated glass from the replacement of windows and windscreens.’ In total, some 300 tonnes of solid waste have been collected in 2024 at the time of writing.
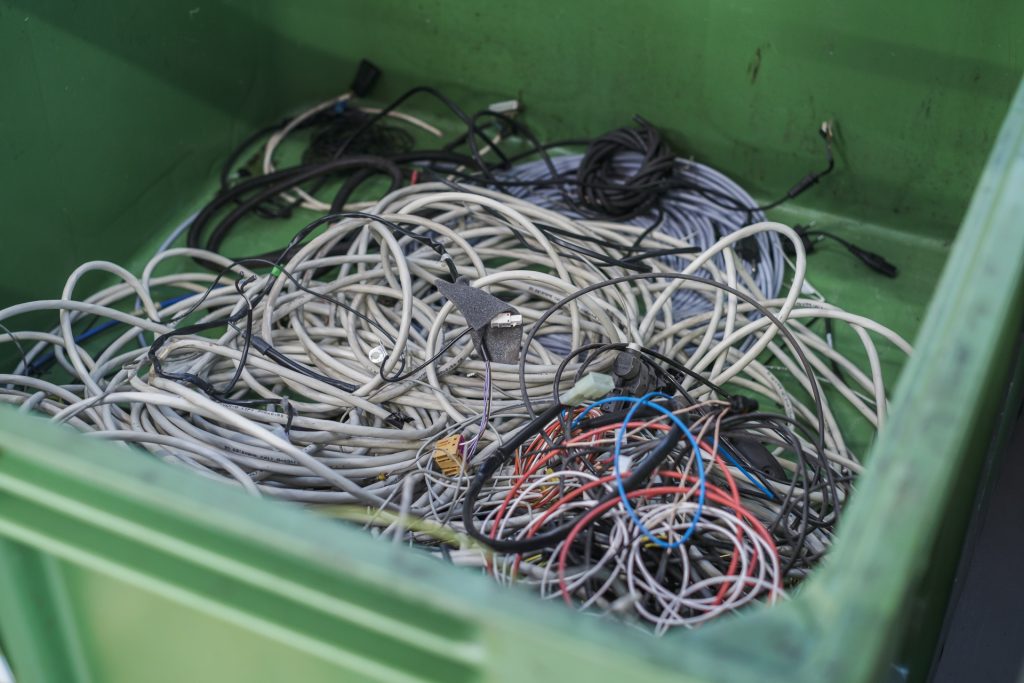
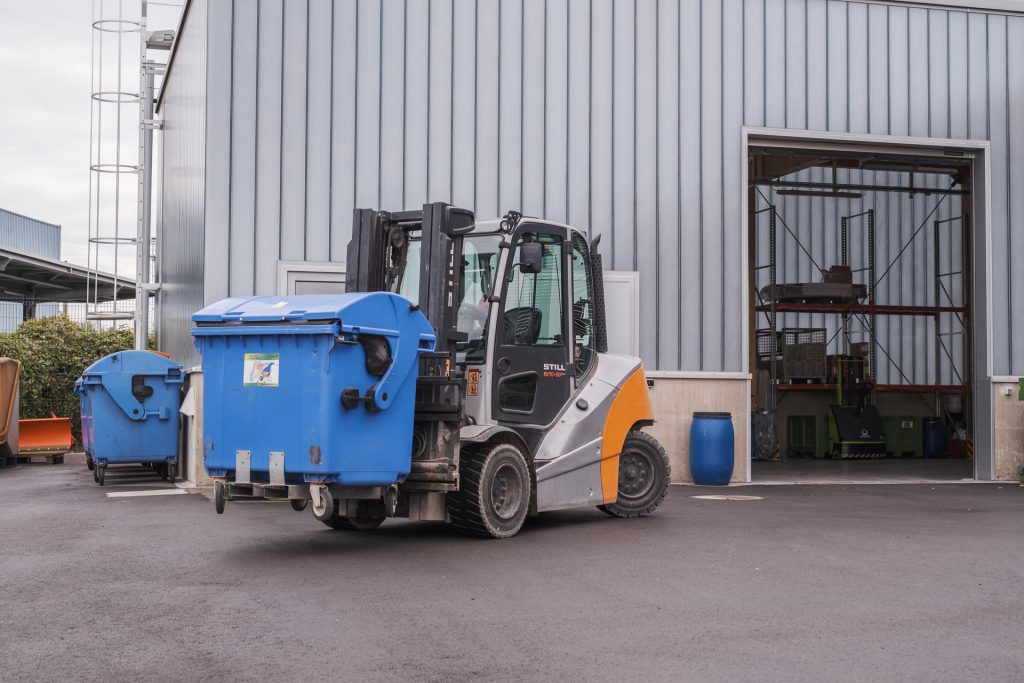
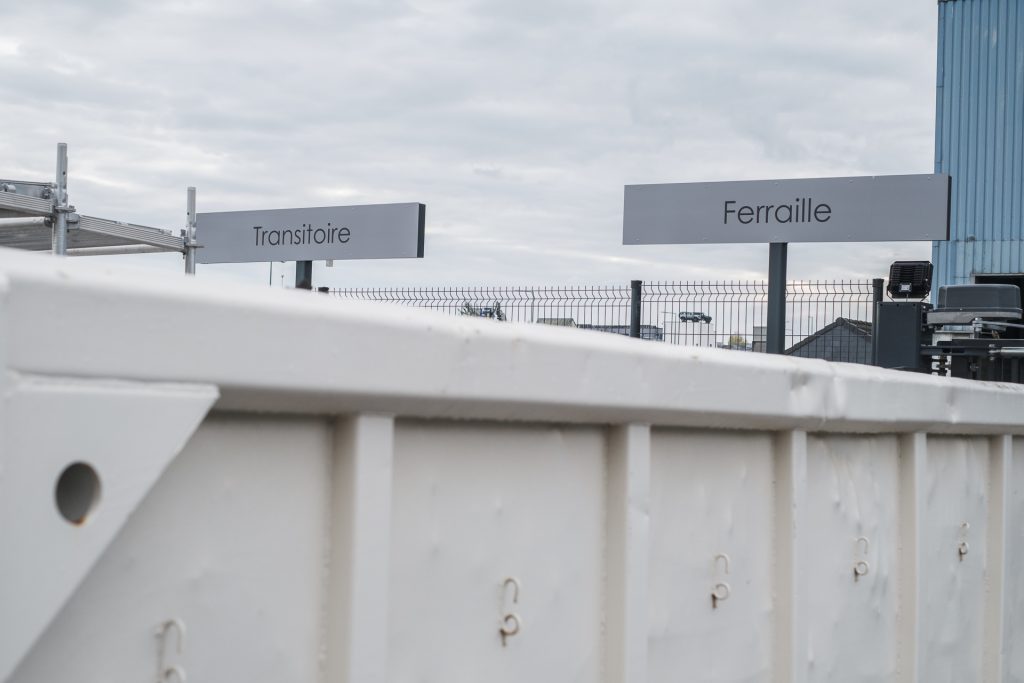
This waste collection is constantly evolving, thanks to the long-standing dialogue and collaboration with the main partner: SDK fir Betriber, which emerged from the SuperDrecksKëscht.
Patrick adds: ‘We are already familiar with the electrification of the fleet of road vehicles or buses at our level, as we usually receive various types of used batteries from rolling stock. Since this year, we have also been accepting bogie shock absorbers (the part on wheels on which the bodies of passenger wagons or railcars rest), making it possible to recycle these parts, which are mainly made of iron.’
Continuous improvement also applies to the organisation of the sorting centre, for example by equipping it with specific tools to contribute to the health and safety of its employees. One example is the recent purchase of a manual lifting crane, particularly useful for handling electric batteries…
Nothing is wasted, everything is recycled, including good ideas.
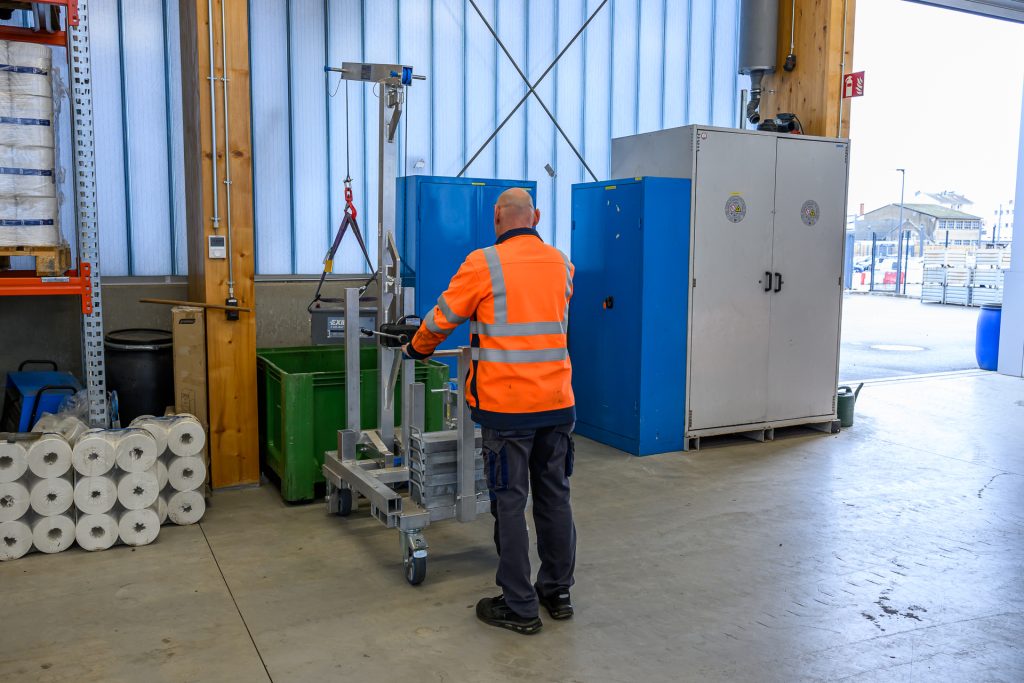