An even more efficient, even more ecological train wash
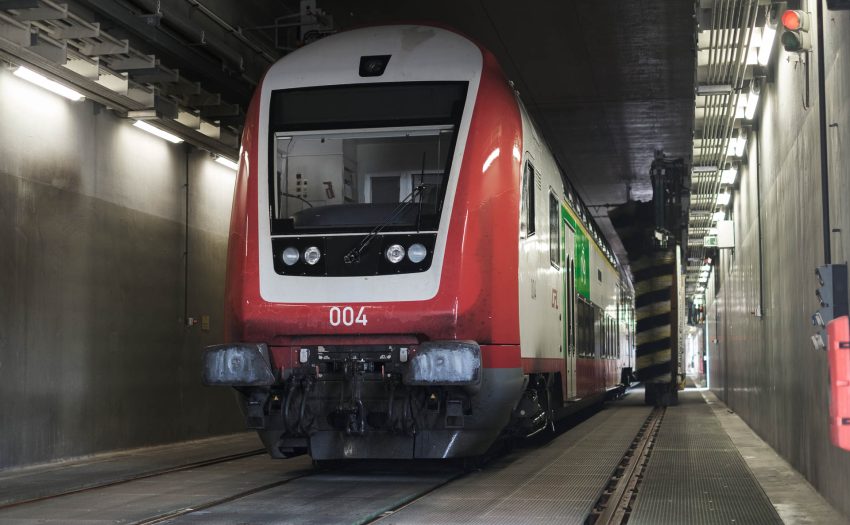
The CFL train wash has just been modernised to handle more trains, while reducing the amount of water used for each train wash. A remarkable achievement by CFL employees, which is a concrete example of sustainable development applied to the railway sector.
More seats to meet customers’ mobility needs means longer trains on CFL lines. While the platforms of railway stations and stops are currently adapted to accommodate them, the same is true for other maintenance or repair infrastructures.
This is the case for the CFL washing station located in Bonnevoie, which has been managed by the CFL Infrastructure Management since its opening in 2018, in parallel with the new Central Workshop.
“The station is now ready for use in a few seconds.“
Mike Feinen Maintenance Manager Washing at the CFL Operations Centre.
After five years of operation, the team of 3 employees at the CFL Operations Centre took into account their own feedback to start a modernisation programme, in the spirit of continuous innovation and quality improvement promoted by CFL. By taking advantage of the full potential of the cleaning hall.
“The in-house modernisation has enabled us to modify the cleaning software to optimise its operation and, as a result, to allow our customers to travel on trains that are regularly serviced and available quickly after arrival,” says Mike Feinen, Head of Maintenance and Washing at the CFL Operations Centre. “The system also performs live monitoring of energy consumption and is able to detect any anomalies that may occur in the train, for example if a door is open or not properly closed when it enters the cleaning hall.
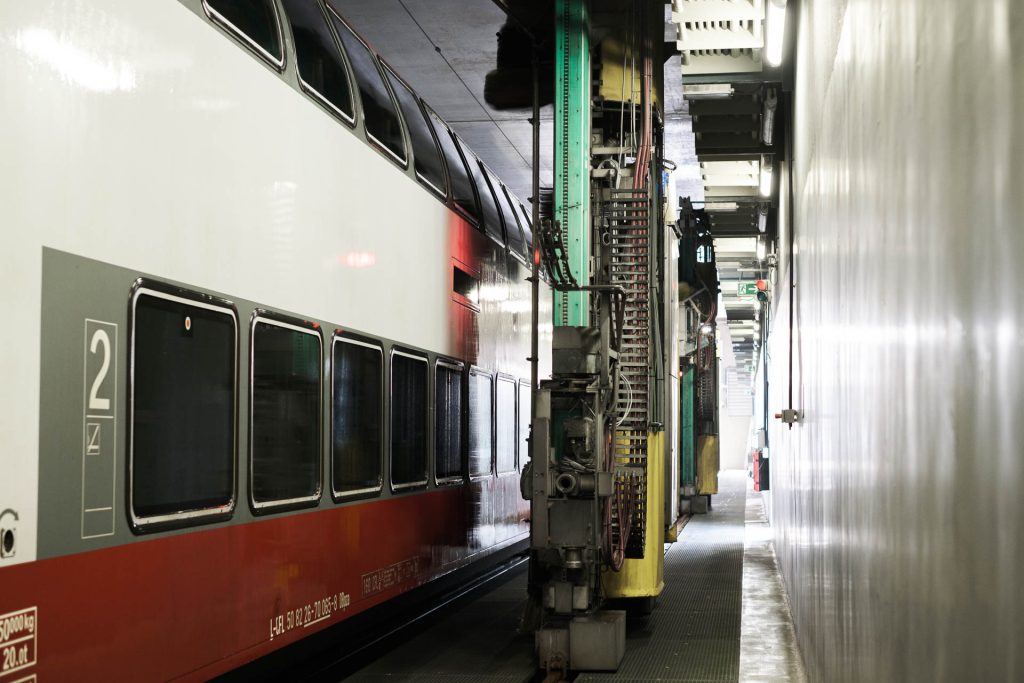
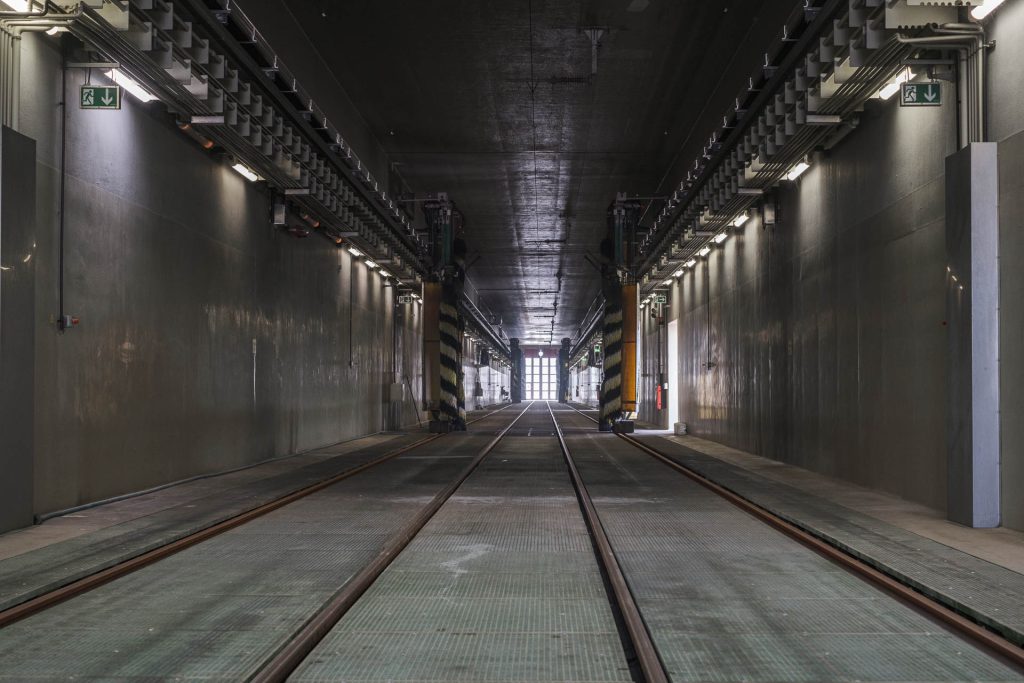
50% less washing time
Another direct benefit is a 50% reduction in wash time from 60 to 30 minutes. No matter how long the train is. “The station is now ready for use in a few seconds, compared to 10 minutes with the old software.”
“So far, we are gaining around 25% efficiency in terms of handling capacity, since we are washing more than 500 metres of train per day, compared to 403 previously,” adds Mike Feinen. “We consider that we have a margin of up to 800 to 1,000 metres of train per day.
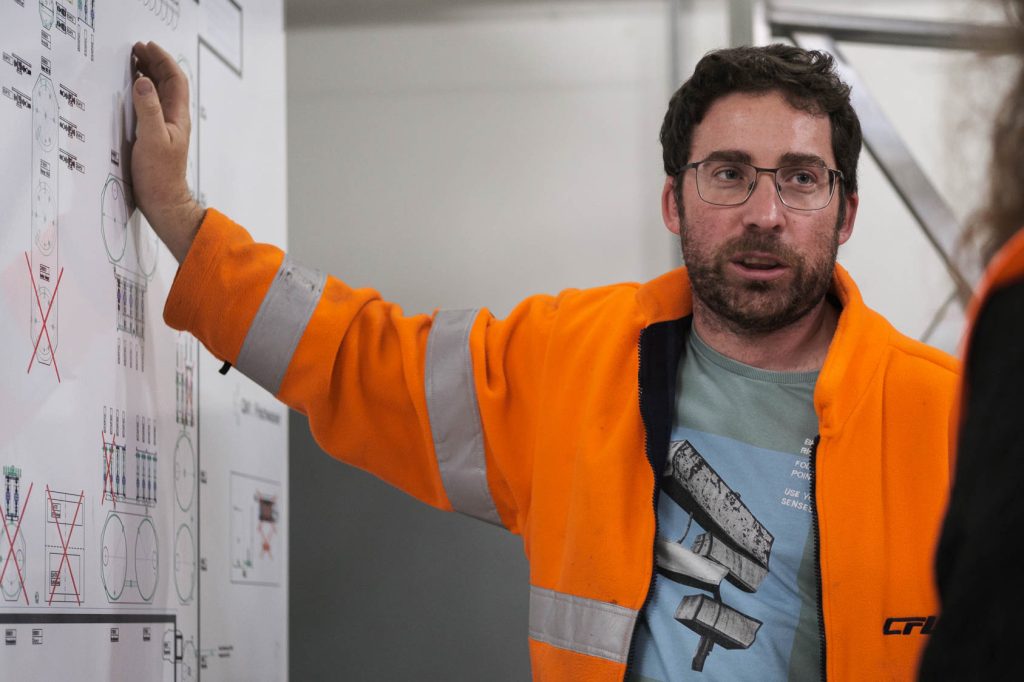
“The water we use is recycled through our biological treatment plant.“
Mike Feinen Maintenance Manager Washing at the CFL Operations Centre.
The attention to the use of natural resources and the environment has been an integral part of the operating philosophy of the car wash from the beginning with the use of a neutral cleaning agent.
91% less water consumption
A new milestone has been reached in this modernisation by reducing fresh water consumption from 40-60 litres per metre of train to 3-5 litres, a saving of 91%.
“The water we use is almost entirely recycled thanks to our biological purification plant, which is located in the basement and recovers waste water,” explains Mike Feinen. “The water runs in a closed circuit with a capacity of 140,000 litres. We still need a few litres of water to compensate for evaporation, especially in the summer, and drag water.”
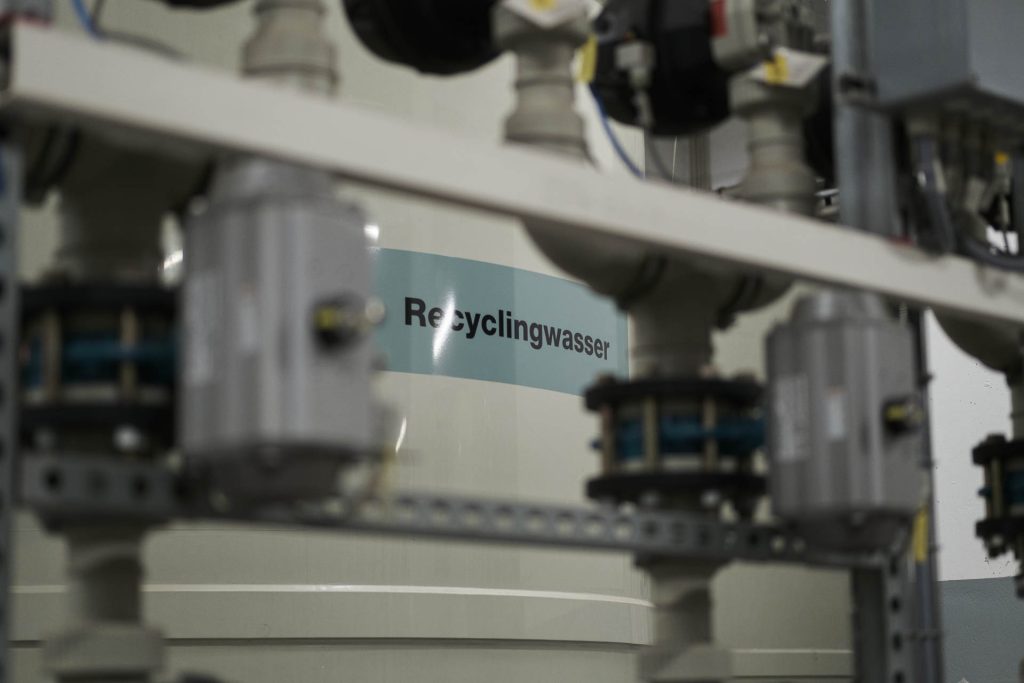
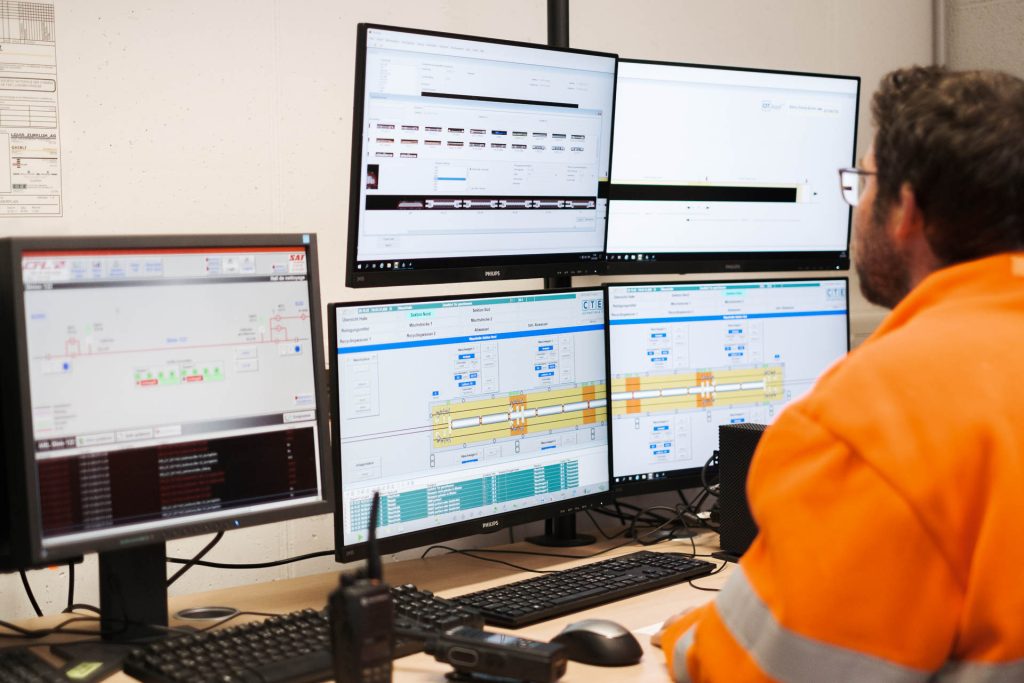
The fully automated washing station handles all the CFL trains and offers its services to foreign railway companies such as SNCF, which uses it for its TGV trains passing through Luxembourg.
An average of 8 railcars pass through the station every day, depending on their state of cleanliness.
To discover the backstage of the washing station: