The tamping machine: Millimeter work on the track
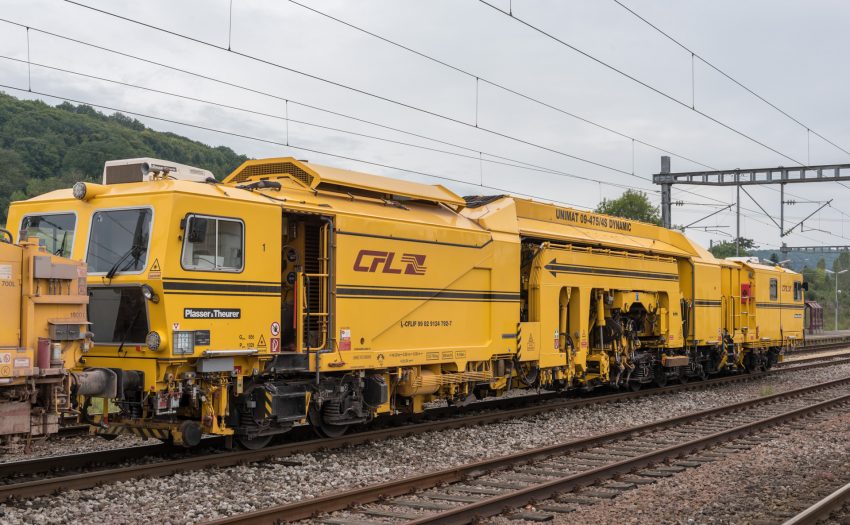
To ensure that customers can travel comfortably and safely by train, the CFL works non-stop on the maintenance and repair of Luxembourg’s rail network. Heavy machinery is used to help the CFL employees with this work. In a series of blog articles, we will give you an insight into the world of these strong and unique helpers. Today: The tamping machine.
The starting point: the actual and the desired state
The starting point for work with the tamping machine is the track plan: For each track, there is a plan that states how and where it has to be placed, so that the safety and comfort of the customers can be guaranteed. This is the so-called desired state. It is different from the actual state, which, by measuring the track, shows how the track is currently positioned and how it compares to the desired state. This data is measured with the help of marking points on the poles next to the track and transmitted to the tamping machine. In case of a difference, the machine compensates for the gap between the target and desired state. Last year, the tamping machine repaired 85km of track in this way.
Millimeter work on the track
A distinction is made between a tamping machine that lifts and moves tracks, one that does the same for switches and one that combines both functions. The CFL have the latter.
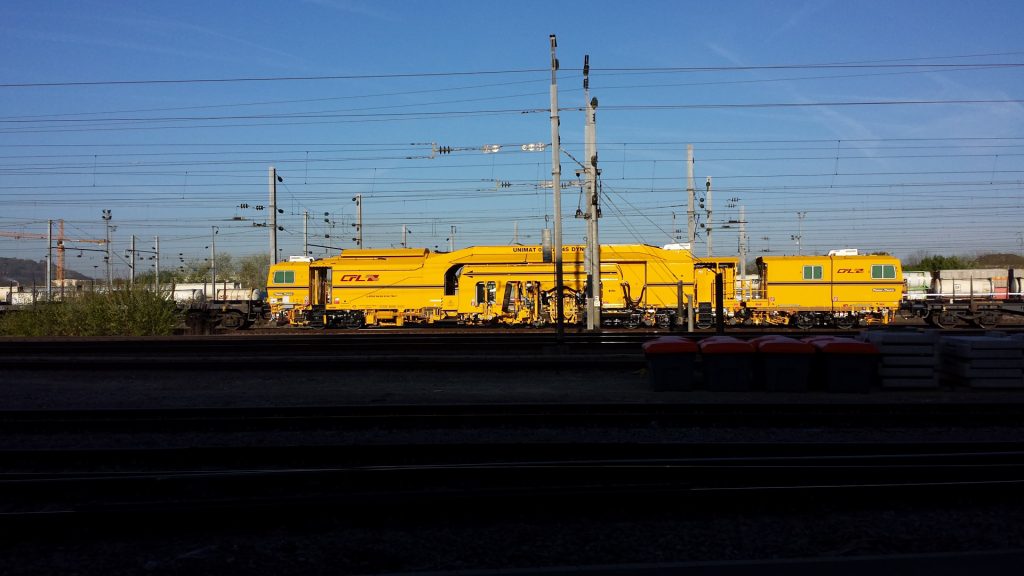
The CFL never use their tamThe CFL never use their tamping machine to install new rails and sleepers, but only for repair and maintenance work. The goal: to always meet the highest safety and comfort requirements. This can be guaranteed by ensuring that the track is always in the desired state, i.e. in the optimally intended condition. Slight differences are caused by various factors, for example, vibrations during train operation, the weather, e.g. in the form of major precipitation, or poor soil, such as clay. Due to its properties, can sink, together with the ballast. In such cases, the tamping machine comes into play.
How does the lifting and moving of tracks work?
The tamping machine can raise tracks and move them sideways. To do this, it clutches onto the rails and lifts them up together with the sleepers. Tamping picks then drive out, pushing additional ballast into the track bed to create a new support for the sleepers. Then, the rail is put back in the correct position. This is millimeter work: a tamping machine lifts between 10 and 60 millimeters during an operation. Sideways, it can also move up to 30 millimeters. That may not sound like much, but it involves lifting an enormous amount of weight and, at the same time, taking care that nothing is damaged.
In order to bring a track that has sunk back into the target position, new ballast is needed. For this reason, a ballast wagon always drives over the respective tracks before a tamping machine is used. Due to the delivered additional ballast, the tamping machine is able to stabilise the respective track. After that, a ballast plough repairs the tamping holes left behind – true teamwork!
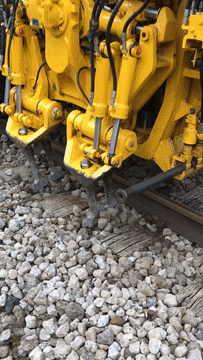
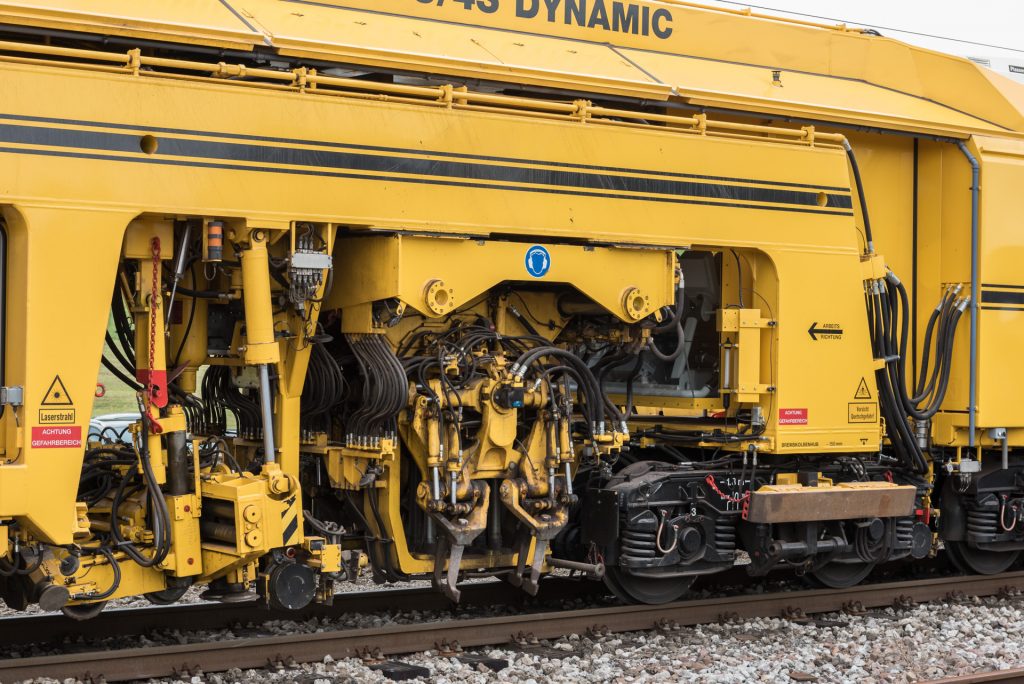
Regular inspection for the customer’s safety and comfort
Twice a year, the CFL commissions the Deutsche Bahn (DB) to drive a track recording car over the Luxembourgish railway network. This is a special wagon that measures the actual state, identifies differences between the actual and desired state and provides information about necessary maintenance work on the track. By coordinating the operating plans of the track recording car and the tamping machine, the repair work can be started immediately after the measurement has been deployed.
Temperature as exclusion factor
Operations can only take place at a rail temperature between 3 and 35 degrees. Only in this temperature range can the work be carried out without danger to the machines and the track infrastructure.