Air conditioning on board trains: a cool thing
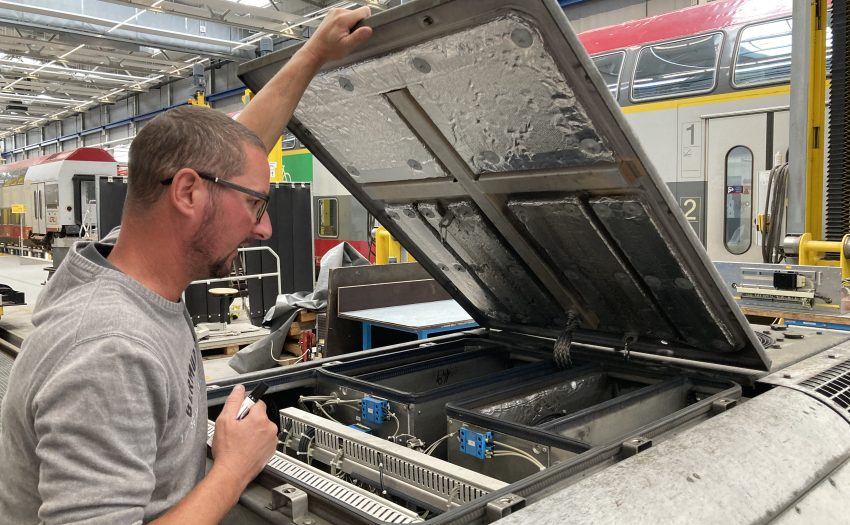
Whether in summer or winter, air conditioning in trains is an essential part of customer comfort. At the other end of the ventilation system, a team of CFL refrigeration experts is in constant action. Meet the experts who keep their cool under all circumstances.
Welding, electricity, electronics, mechanics and the all-important refrigeration techniques… all together in one team. Welcome to the premises of the CFL experts in charge of the air conditioning systems (cooling and heating) installed on board rolling stock (with the exception of the older generation Z2 railcars).
Based in the Central Workshop of the CFL Repairs and Maintenance Centre, this team of a dozen people works at a fast pace. One key figure summarises the scale of the work carried out by these refrigeration engineers: 850, the number of air conditioning units that accompany customers on their trains. And to ensure that the journey runs at the right temperature, anticipation and a certain discipline are essential.
“We handle the entire chain within our scope of work, from installation to maintenance or repair to replacement or updating of air conditioning units,” explains Steve Seidel, Air Conditioning Team Leader at the CFL. “Planning preventive checks, maintenance and the statutory annual refrigerant leak test, documenting past work and communicating with other departments are all key to carrying out the maximum number of operations without interrupting the end service to the customer.”
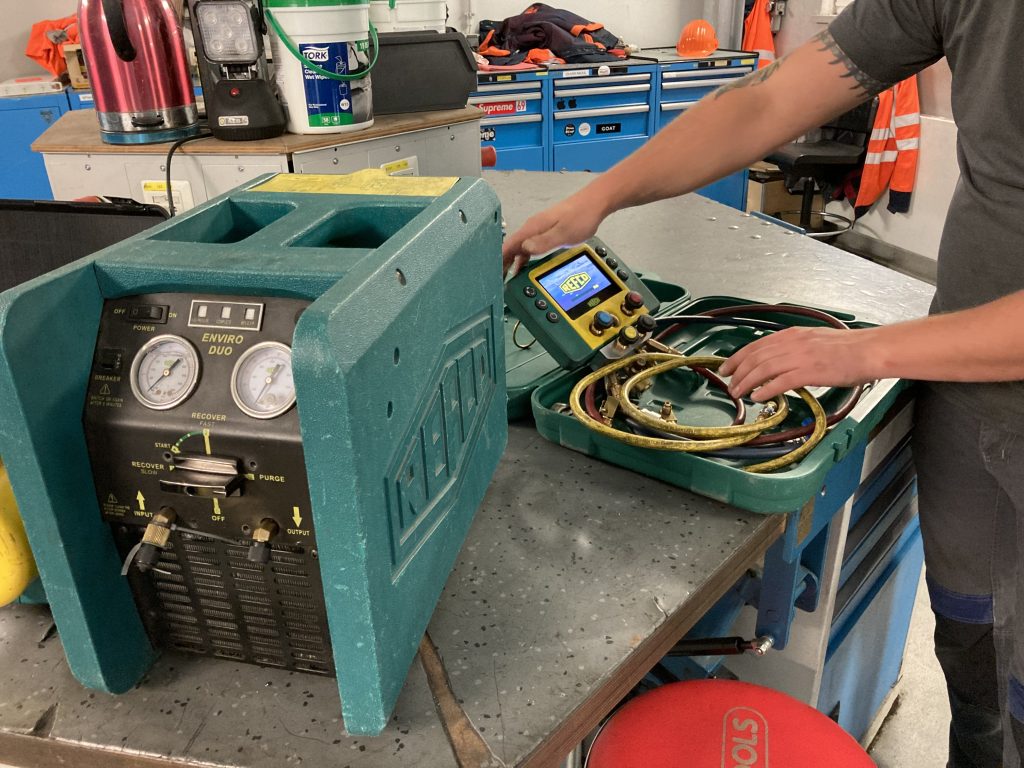
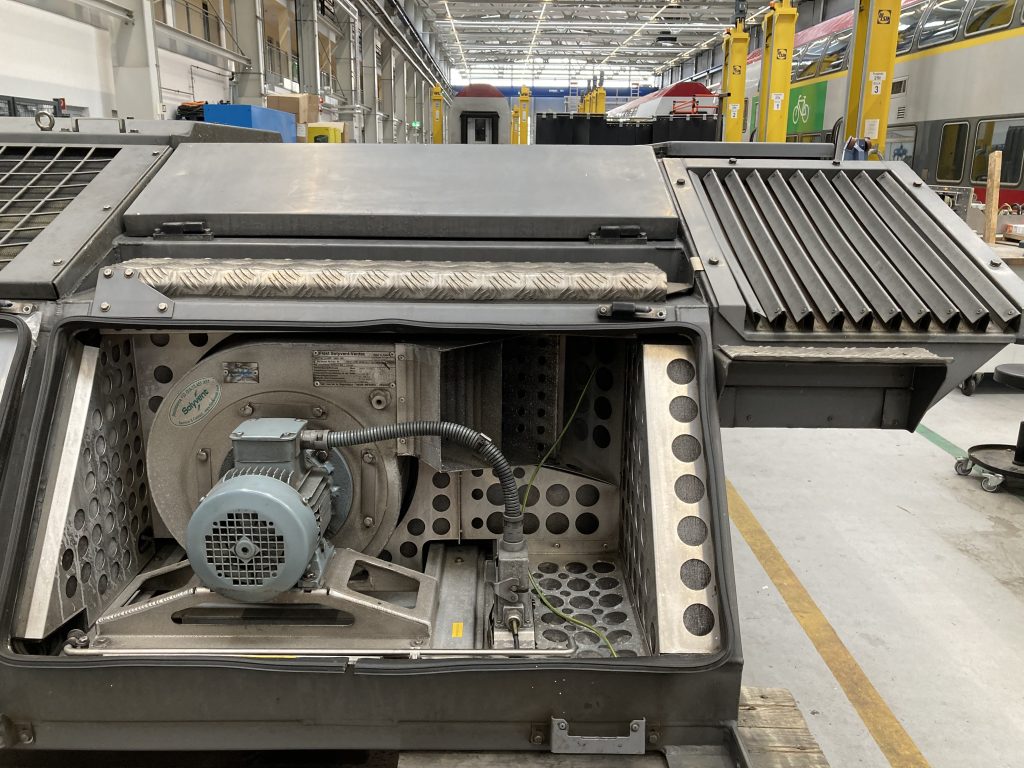
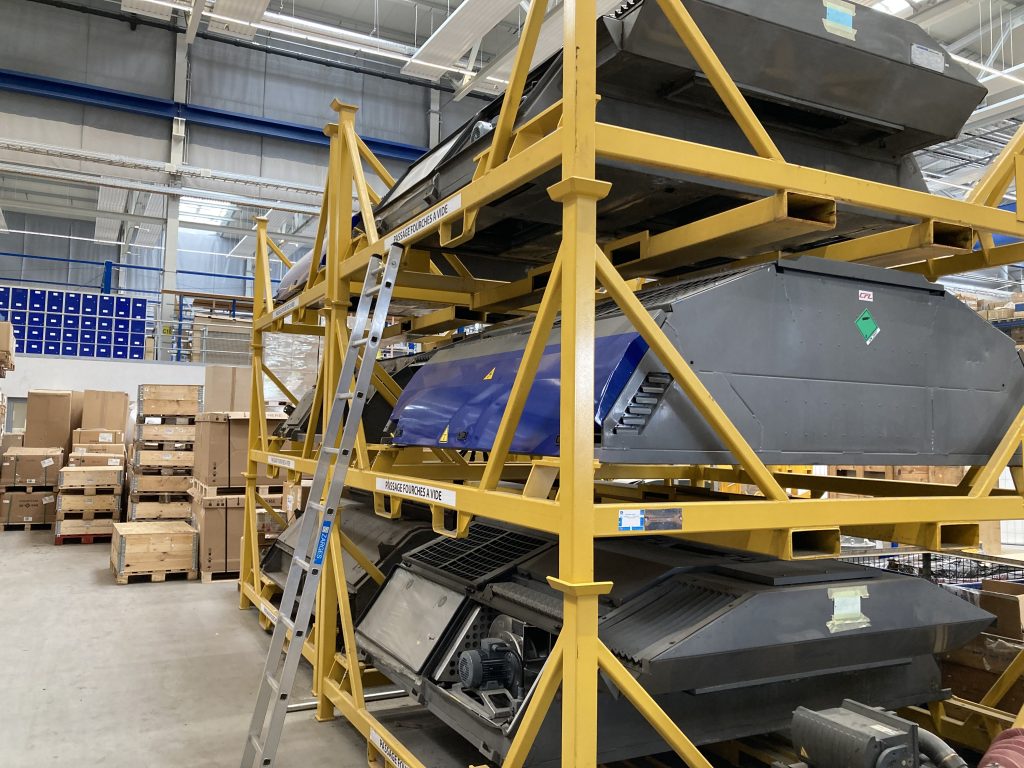
But how does air conditioning work on trains?
The configuration and components of the air-conditioning units vary depending on the rolling stock, and are located either in the cab or on the roof.
As for the actual adjustment, this is carried out by the train crew according to the desired interior temperature. “Sensors provide the external temperature information to the system, which adapts its operation to provide the best performance,” adds Kim Weyland, Air Conditioning Team Leader at the CFL. Each half of the car has its own temperature control system that can be adjusted as required.
“Just like the refrigeration or air-conditioning systems in a house, our systems recover the heat emanating from the compartments via vents located in the passenger compartment. This heated air is sent to the air-conditioning unit in the roof, where heat is exchanged or the air drawn in from outside is cooled,” explains Steve Seidel. “The specificity of our equipment comes from a set of additional parameters required for the railway environment, particularly in terms of safety”.
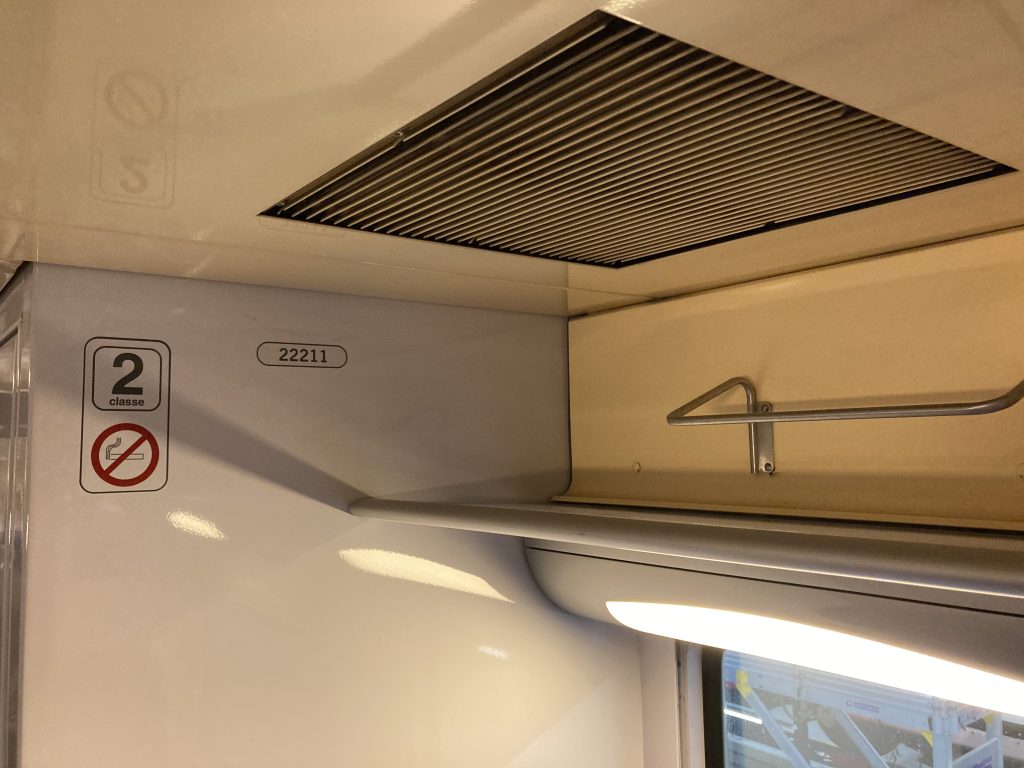
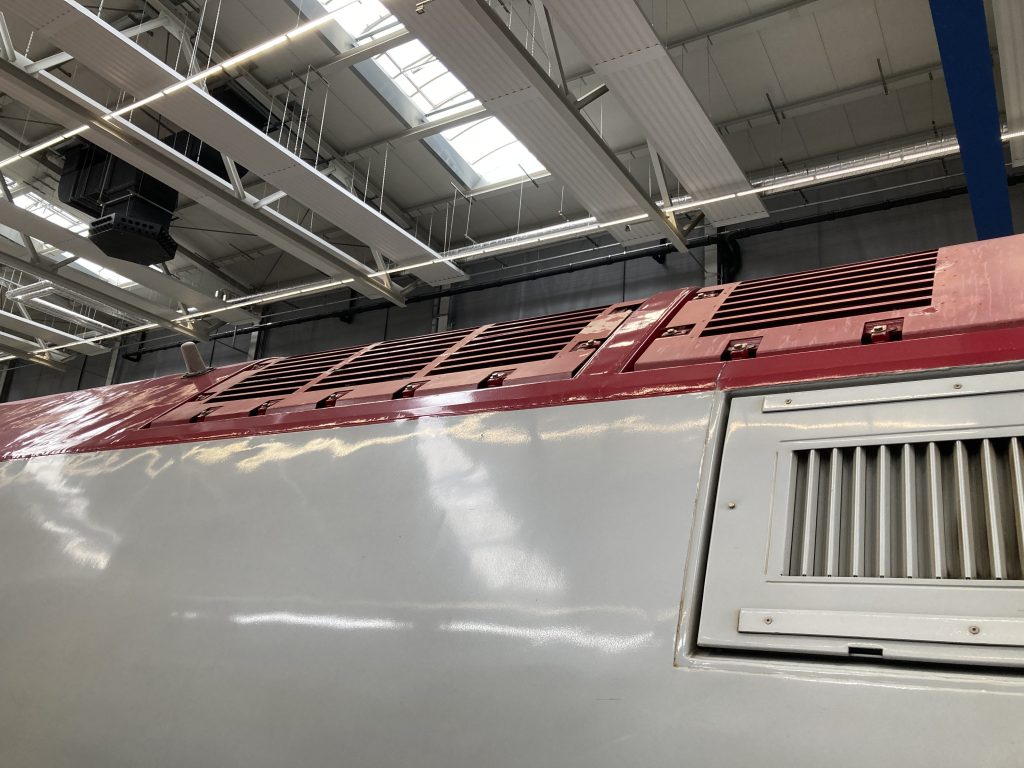
The team of refrigeration engineers, which has access to predictive maintenance tools, also keeps a close eye on developments and innovations in the production of liquid refrigerants, with a view to ensuring maximum respect for the environment. A recycling circuit has also been in place for several years, with the collaboration of the CFL sorting centre and an external company responsible for taking back and processing used refrigerant liquids.
A new climate to take into account
Although the weather of recent weeks, with its rain and cooler temperatures, has given them some rest, refrigeration engineers are increasingly aware of the effects of global warming on their equipment. Given this new situation, they are taking advantage of any lulls in the heat or school holidays – synonymous with lighter rail traffic – to carry out preventive inspections. “We’re noticing that summer temperatures are increasingly tending to start as early as May, with periods of high heat more marked than in the past,” notes Kim Weyland.
We’re constantly juggling different physics and chemistry subjects.
Steve Seidel, Air Conditioning Team Leader at CFL.
Whether it’s an emergency service outside or maintenance work scheduled when a train is passing through the Central Workshop, the customer and his or her comfort are always on the minds of these behind-the-scenes workers. Both in summer and in winter, when heating is required.
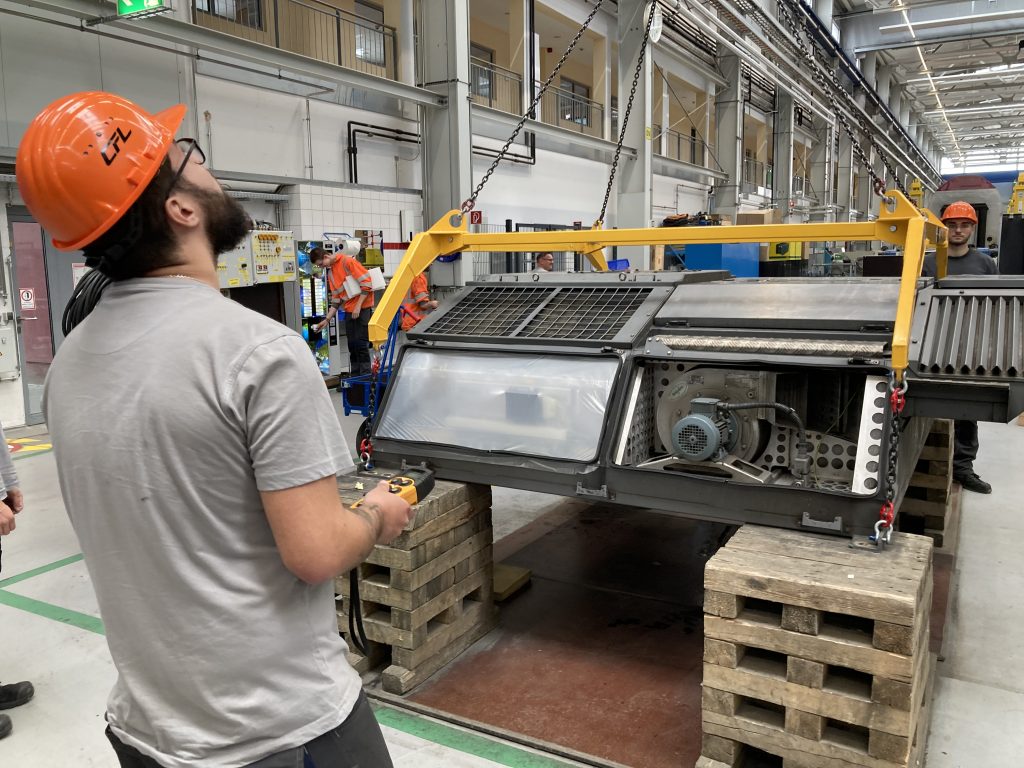
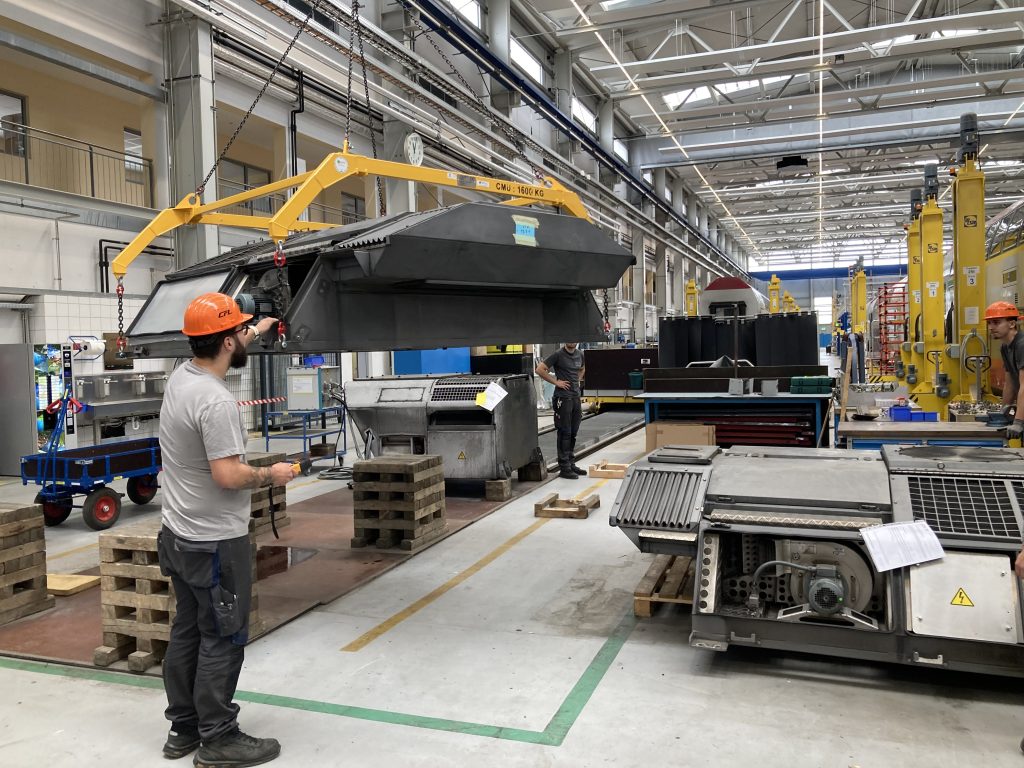
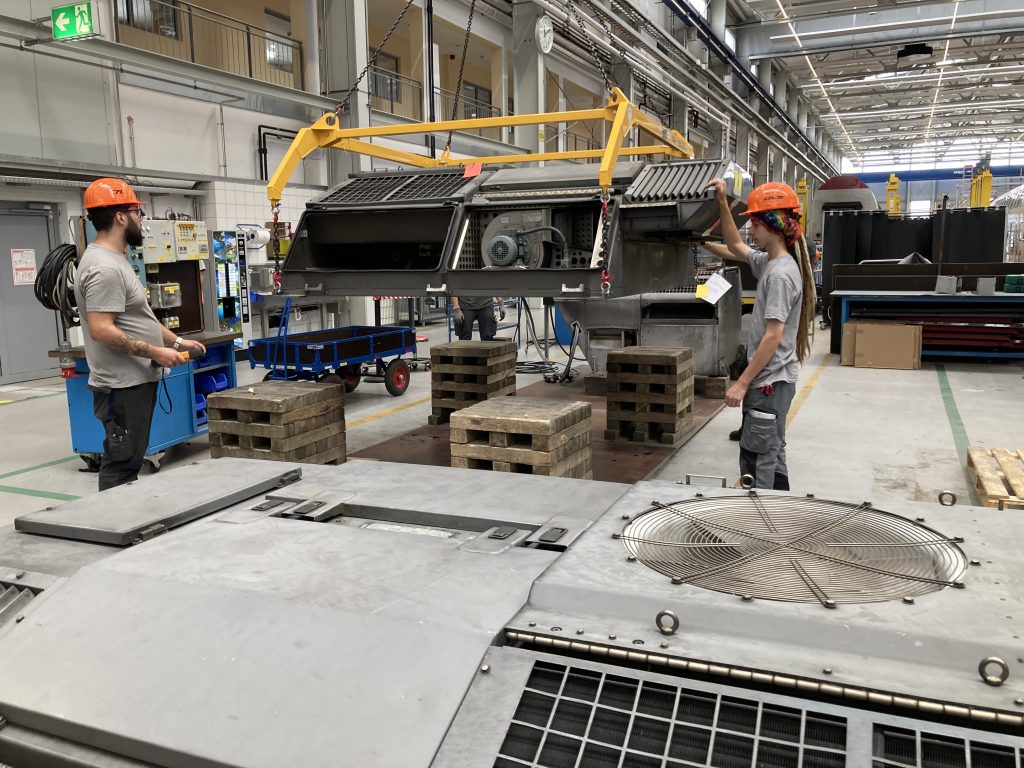
“We work hard to achieve our objective: to ensure that the rolling stock is available as quickly as possible for our customers and to avoid breakdowns,” adds Kim Weyland.
“We’re organised into three shifts and we’re constantly juggling different physics and chemistry subjects. There’s no shortage of work with the expansion of our rolling stock and the evolution of techniques,” adds Steve Seidel, who was the first refrigeration engineer to be hired at the CFL 21 years ago, before laying the foundations for this team.
“At the time, I was one of the first refrigeration engineers in Luxembourg. We really started the air-conditioning adventure with the TER2N-ng series and the 2100 series. These were the first railcars to be fitted with air conditioning, before virtually all our rolling stock was equipped with this comfort, which is appreciated by our customers on a daily basis”, adds Steve Seidel, who today manages a team of 12 people with Kim Weyland and Daniel Schmit.
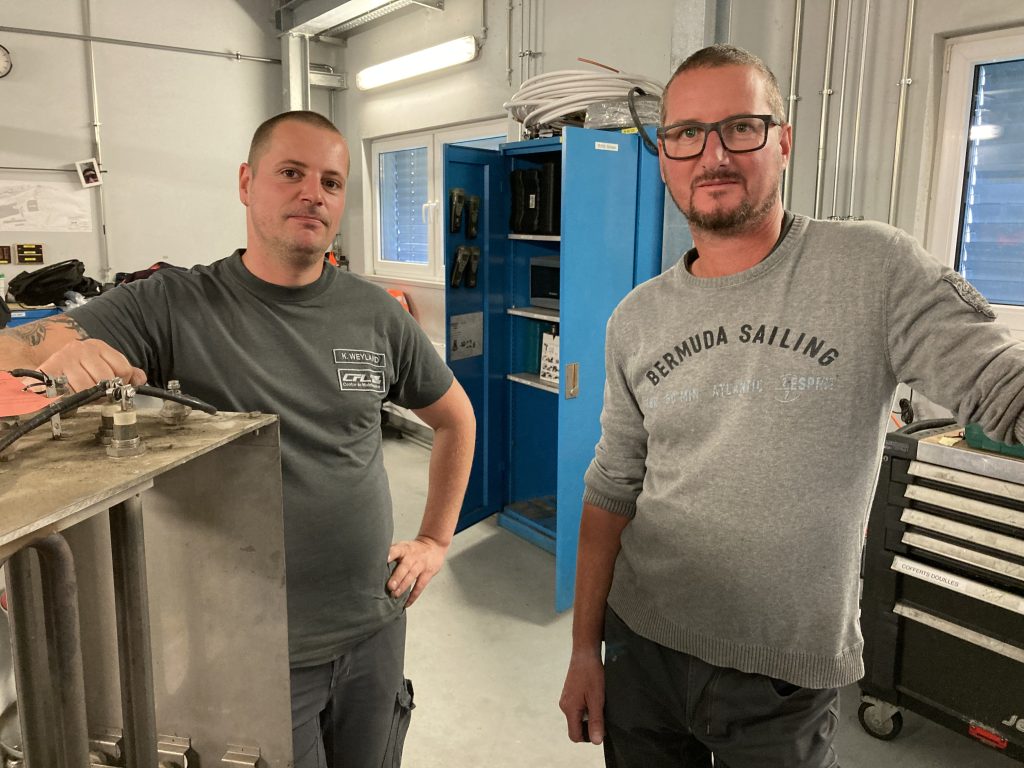
When you meet former refrigeration apprentices who have become CFL agents, and observe the good atmosphere within the team, you can’t help but notice a passion that is definitely contagious.
For this refrigeration profession and many others, the CFL welcome apprentices who can find a future professional outlet in the railway world. Consult apprenticeship offers via this link and job offers via Jobs CFL.